How RTA’s Shop Management System Improves Efficiency
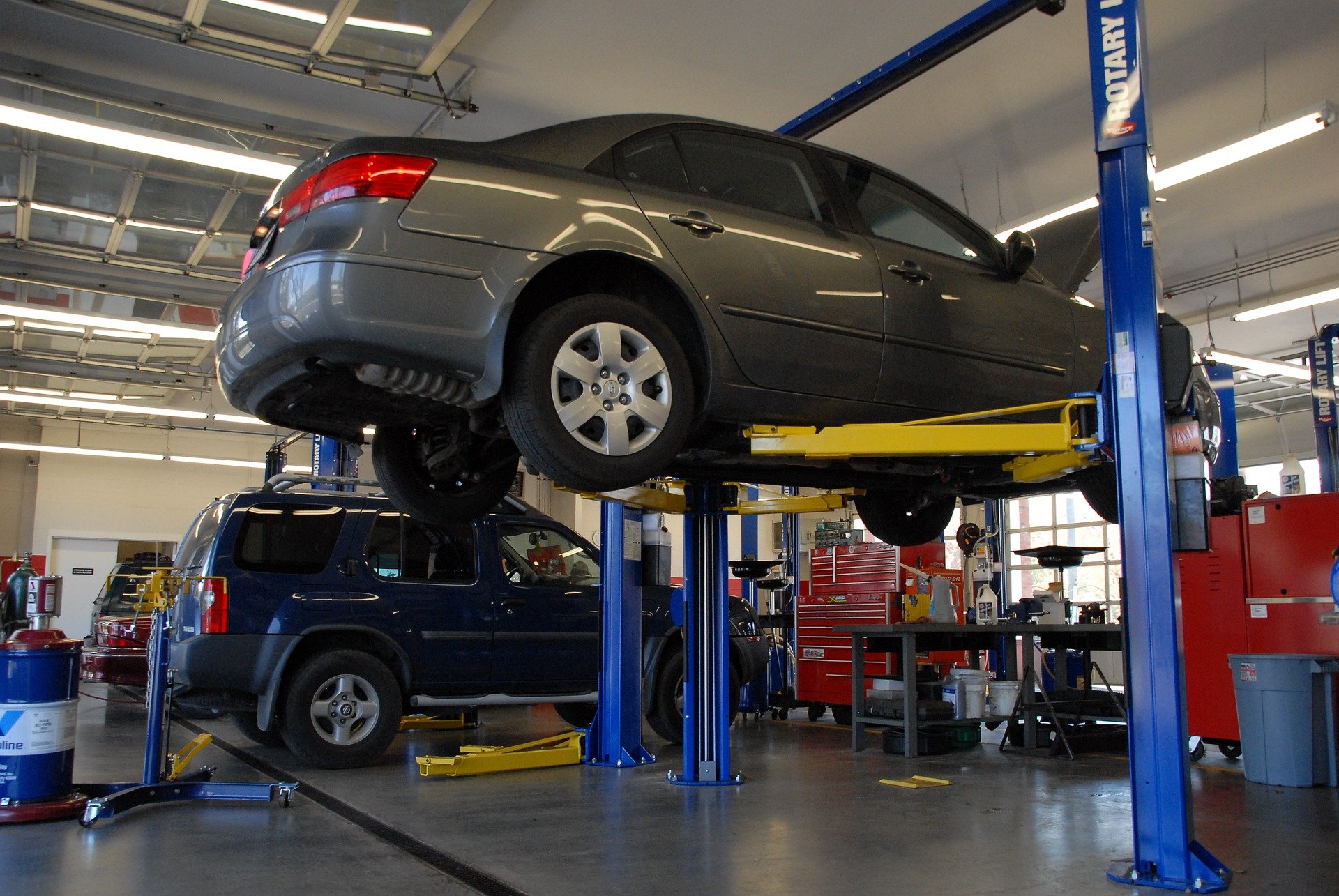
Fleet management efficiency is greatly improved by successfully automating as much of the work process as possible and utilizing the remaining time for priority items.
The RTA Shop Management System has features that will greatly improve efficiency in your shop by providing accurate and quality information to your managers and technicians.
Here are 4 ways our Shop Management System works for you:
1.) Your technicians are the shop's most important assets; RTA gives you the ability to schedule these assets in the most productive way. With the Shop Management System, you are able to track each and every minute and determine where time should be spent. The system frees up technicians from paperwork and allows them to do what they are hired to do: work on vehicles. It also frees up runners from going for last minute parts because the inventory is better stocked.
2.) RTA’s Shop Management System tracks parts usage and allows for a more accurate inventory. This information cuts overall costs of inventory and provides an opportunity to expand the sku selection at the same time. The sku scanning and bar code system eliminates hand written errors, increases efficiency and saves time.
3.) RTA’s “Note” feature allows technicians to leave notes on the work orders as they progress through the shop. This is an excellent feature that saves valuable time by providing anyone with the ability to step in and know exactly what has been done on a vehicle and where the technician was in the process, as well as if parts have been ordered and the overall status of the repair.
4.) The Shop Management System allows for the creation of a customized preventive maintenance schedule, work orders, fuel usage tracking records, detailed maintenance histories, tire logs, accident and claim records, inventory tracking as well as monitoring labor, invoicing, and stock reports.
Here is an example of a Preventive Maintenance Checklist:
VEHICLE PM SERVICE – DAILY SAFETY CHECKLIST:
- Walk around vehicle
- Check for body damage
- Check tire wear and inflation
- View under vehicle for wet spots caused by a possible fluid leak
- Check fluid levels to include engine oil, coolant reservoir level, and windshield washer fluid level
- Review and check the vehicle owner’s operation manual for directions on specific vehicle operations and
- Maintenance items
PM SERVICE CHECKLIST TO BE PERFORMED EVERY 5000 MILES OR ONE YEAR:
- Replace engine oil and filter
- Check/clean battery terminals
- Lubricate/grease all grease fittings including all U-joints
- Check all fluid levels and fill as necessary
- Battery
- Radiator
- Power steering reservoir
- Windshield washer
- Master cylinder
- Transmission
- Transfer case
- Differential
- Check all lights for proper operation
- Check all tires for wear and proper inflation
- Check/replace belts
- Check air filter and replace if necessary
- Diesel pickups: At a minimum, change fuel filter annually (preferably in the fall)
PM SERVICE CHECKLIST TO BE PERFORMED EVERY 10000 MILES:
- Perform all items listed on the “A” PM checklist,
- Rotate tires on all light vehicles (under 10,000 lbs.)