5 Ways to Avoid Downtime with Parts Inventory
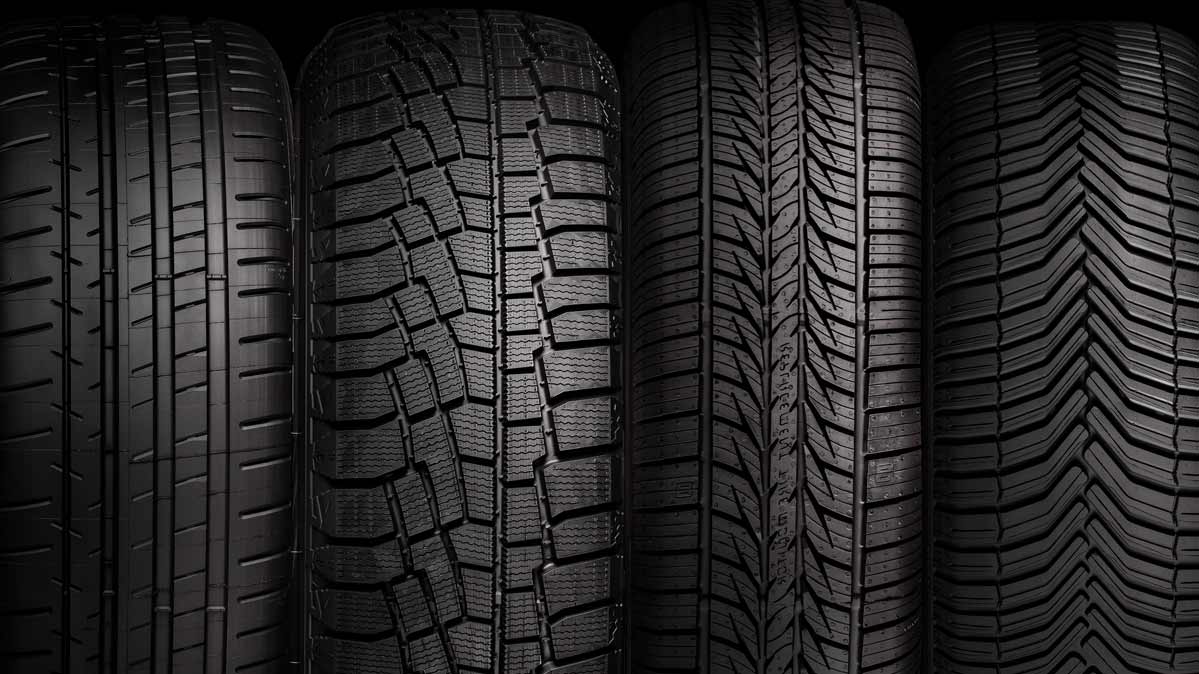
By Mary Gerard, Content Marketing Manager
When your fleet vehicles come in for repairs, how often do you have all of the parts on-hand, allowing the technicians to quickly perform the repairs and get the vehicle back on the road?
Or how many times does an asset come in and the part isn’t available, so the vehicle needs extended downtime until the part arrives?
This is a waste of time and money for your operation. The technician can’t complete the work order, the driver can’t operate the vehicle, and the parts room needs to rush a part into stock. It creates unneeded stress and can even result in extra costs if the part needs to be expedited or if a technician needs to work overtime to complete the repairs as soon as possible and get the vehicle back on the road.
Fortunately, there are ways you can avoid these situations.
Implement a Parts Inventory Management System
Create a reliable parts inventory system. You can get help with this by using a fleet management system. This will let you quickly and accurately track your parts inventory. An FMIS can give you real-time visibility into your stock levels, automatically trigger reorders when inventory reaches a certain threshold, and generate reports on inventory usage and trends. This will help you proactively get the most-used parts back in stock, and avoid parts shortages.
Take Regular Parts Inventory
Perform regular audits on your parts inventory. Take a count of each type of part and check its condition. This will help you verify what’s on the shelves versus what’s in the software system. This will also help identify any discrepancies, such as missing or misplaced parts. By keeping an accurate parts inventory, you should always know what parts are in stock. This ensures you have the parts you need for a given repair, reducing a vehicle’s downtime.
Establish Relationships with Reliable Suppliers
To get parts when you need them, you need to build strong relationships with reliable suppliers who can deliver parts on time. Work with your suppliers to understand how much lead time they need to deliver a part, what their order fulfillment process is, and anything that could lead to delays in getting the parts you need. Establishing a close relationship with them will allow you to get the parts you need – when you need them. This can help avoid vehicle downtime.
Monitor Data
Using an FMIS, you can pull the data you need to check stock levels, track parts performance to help determine when parts might need to be replaced, monitor vehicle preventative maintenance schedules to ensure PM parts kits are in stock and more. Using this data, you can look for trends and get a better idea of when you need to order parts.
Plan For Emergency Situations
Unfortunately, emergencies can happen. From weather events to natural disasters, crises can cause vehicle downtime. To try to minimize the time vehicles are in the shop, you should create an emergency plan that includes maintaining a safety stock of critical parts, naming backup suppliers in case your preferred vendor isn’t operating, and ensuring your staff is trained on how to handle emergencies and what to do to get vehicles back on the roads as soon as possible.
Putting plans in place can help you ensure you have the parts you need to get your vehicles repaired quickly and back out on the roadways. If parts are not in stock, vehicles will need extended downtime while the shop is waiting for the parts to arrive. This can be costly – as you spend extra in labor and parts acquisition costs.
See why RTA’s parts inventory module is the best in the industry. Schedule a free demo today!