Fleet Exception Analysis: Do Peaks and Valleys in Your Data Pique Your Interest?
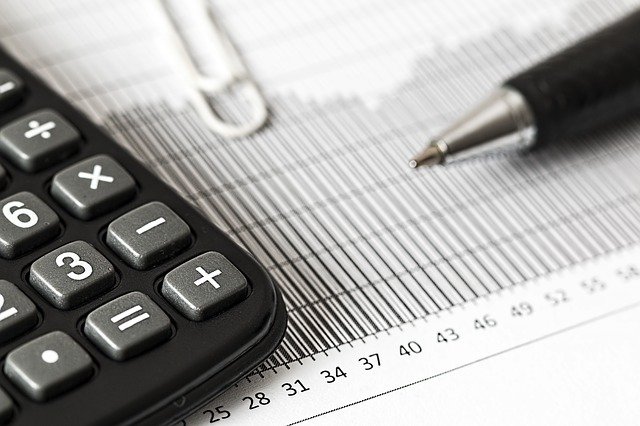
By Steve Saltzgiver, Fleet Success Ambassador
As fleet manager, my favorite task was to review data sets and try to make sense out of them to initiate an action to either improve processes, reduce expenses — or both. The ability to use data as a mechanism to better understand what’s happening and to continuously improve your fleet operation is critical to fleet management. One of the challenges in today’s fleet management operation is the inability to review data trends due to the loss of Baby Boomers exiting the workplace for greener pastures (i.e., retirement).
Most Boomers had a sense of what data means, as they understood fleet management in a perfunctory – how to repair and operate a vehicle – sense. Boomers were much more “hands-on,” often growing up in the world of fixing vehicles (e.g., grew up fixing cars, had shop classes in school, helped parents repair family cars, etc.). Today, this “hands-on” opportunity has virtually diminished as repairing vehicles has become more of an academic or analytical exercise.
The latter gave Boomers inherent advantages to recognizing and understanding data. This said, the current generation is far more advanced in analytical skills, which gives them an advantage if they can acquire a few perfunctory skills to better understand how vehicles are used, repaired, maintained, and how vehicles function to perform various mission-critical tasks.
As a Boomer fleet manager, I recall many times where data analysts would present me with charts and graphs, like Figure 1 above. I would first focus on selecting a few units (exception report) and proceed to ask them questions like “why is unit 0838 and 0848 taking us 50% more labor to maintain than the other units?” Most often, having not dealt directly with fixing fleet vehicles or repair shop activities, they were not sure how to read the chart, let alone answer my question. As a fleet professional, let’s look at this graph and see how we might better understand and potentially resolve any issues.
Problem Analysis
In previous blogs, I’ve spoken about a common problem-solving technique in analysis which includes data sets is to start asking, “WHY”[1]. Most often by the time one asks “WHY” five times they better understand the issues and are more apt to solve an issue.
Let’s start with unit #0838, which has logged 77.66 hours of labor for a 12-month period compared to the average of other units well below 50 hours:
- WHY do we think these hours are so high, what does the data show?
Answer: This unit operates as a motor pool unit where multiple drivers are frequently using this vehicle.
- WHY do we think this motor pool unit takes more 50% labor to maintain?
Answer: Multiple drivers fail to take personal ownership while operating this unit and fail to operate the vehicle responsibly.
- HOW could we reduce the number of driver misuse or abuse-related repairs in the future?
Answer: We could step up the requirements for motor pool vehicle drivers to complete a detailed inspection (DVIR) to note and record any previous defects prior to operating.
- WHAT does the excess labor show us in the way of abnormal repairs?
Answer: This unit has been involved in several minor accidents where miscellaneous body damage [i.e., driver(s) misuse, abuse] which had to be repaired by the technicians. There were also several repairs related to interior cleaning, tire wear, and tire air pressure that may be avoided with improved inspections and communication.
- WHO repaired this unit, and do we see any trends relating to lack of training, quality, or needed resources to reduce labor time in the future?
Answer: We reviewed the tech work orders and found two techs that performed the bulk of the work and we found one technician who could use additional training to perform more consistently to established repair times. We have scheduled this tech to attend a training class ASAP.
So, after asking yourself these five questions, what did we learn about this data?
- We learned motor pool assigned units require more maintenance and repair due to the nature of their mission. Moreover, these units may require additional analysis to create a separate Vehicle Equivalent Unit (VEU) class outside their “permanently assigned to one driver” counterparts to account for the hire costs and resources necessary to maintain.
- We learned motor pool unit operators don’t take the necessary ownership and time commitment related to ensure care and safety of these units, as those in a permanently assigned unit.
- We learned that we had a process or policy gap where we were not requiring or enforcing daily driver vehicle inspections to increase driver accountability for the care and condition of the motor pool units before and after each trip.
- We learned that we may have a repair competency or skill issue where one or more technicians require additional training to adequately maintain these motor pool units.
Conclusions
As shown, these analyses are not as cut and dry as one might expect. The key to being able to conduct these analyses is to have the data necessary to organize it into a structured reporting format to begin posing the five “WHY” questions, causing management to act appropriately. Moreover, having the data at your fingertips in an “exception report,” as shown, reviewing only a small subset of the data allows you to make good decisions. As you continuously focus on the few exceptions, over time fleet managers are better able to get a handle on the issues and avoiding paralysis by analysis.
The need for a robust Fleet Management Information System (FMIS) to capture and analyze data cannot be underestimated. Your credibility as a fleet management organization depends on the ability to use fleet data to initiate continuous improvements that benefit both the stakeholders and the organization at-large. The quick decision demonstrated in this example are just one of the many that can be made having the accurate data housed in one of the industry’s foremost FMIS applications such as the RTA system.
[1] Keep in mind that every question does not necessarily start with the word “WHY”, other interrogatives could also start with “WHAT”, “HOW”, WHICH”, WHERE, “WHEN”, “WHO”, etc.