9 Tips to Get the Most Out of Your FMIS
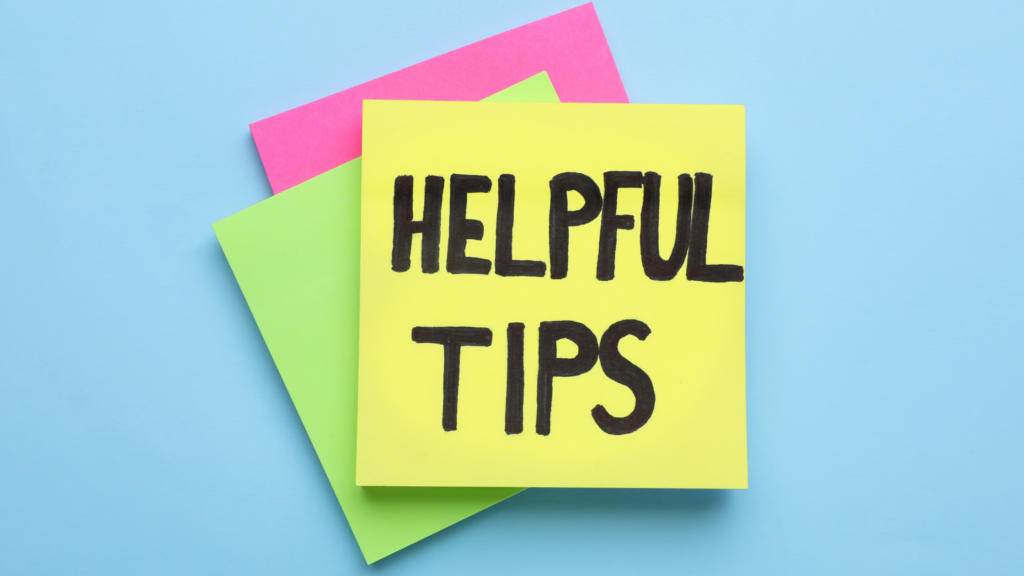
Your fleet management information system (FMIS) is arguably the most important software your fleet has. And chances are, you’re nowhere close to reaping the full benefits this system has to offer.
The right FMIS, when set up well, can:
- Improve asset availability and utilization
- Lower operational costs
- Ensure driver and community safety
- Increase shop productivity and technician efficiency
The list goes on. Your FMIS can help your fleet reach new levels of performance if you leverage its full capabilities, get everyone, put the right data into it, and pull the right data out of it.
Here are nine tips to make sure your fleet gets the most out of your FMIS.
1. Use dashboards to align your stakeholders.
Your FMIS puts a whole world of insights at your fingertips, as long as you’re capturing the right data in meaningful ways.
If you haven’t done it already, start using your FMIS’s reporting dashboards to capture the data that matters to your organization. Dashboards give everyone a shared view of performance and are highly effective at getting stakeholder alignment.
Remember that different people care about different data points. Make it your business to know what data they care about. Then build a dashboard that speaks their language.
2. Train everyone according to their role.
The more your team uses your FMIS, the more benefit your organization will get from the system.
Here’s the thing—everyone uses your FMIS differently. They all have different jobs to do and need different functionality within your platform.
Make sure everyone on your team has the knowledge they need to use the system effectively according to their role. Hopefully, your FMIS provider offers free role-based training or at least has an easy-to-use knowledge base.
3. Set up replacement plans and templates.
Did you know you can manage your asset lifecycle by inputting replacement plans and templates in your FMIS?
Add replacement parameters, all-in acquisition cost, expected life, and reasonable estimates for sale proceeds. If your FMIS has report reminders, use them to make sure you stick with your plans.
Creating a long-term asset replacement plan and sticking to it will help you:
- keep your fleet in the proper shape
- avoid unnecessary downtime
- decrease maintenance and repair costs
- decrease the number of spare vehicles you need
- keep your finance team happy with predictable replacement budgeting
4. Use work order and vehicle status rules and reminders.
You’re probably using your FMIS to track work orders and repairs, but you might not realize you can monitor WO statuses to minimize asset downtime.
Set up your work order and vehicle statuses in your system. Then automate rules and reminders with status changes so you can record how much time each asset or work order spends in each status.
By knowing your current status, you know what’s available right now. But by knowing your averages and bottlenecks, you can predict availability moving forward and use that data to improve your availability rate.
5. Integrate daily inspections into your FMIS workflow.
We can’t say enough about the importance of safety. Driver vehicle inspection reports (DVIRs) are critical to keeping your assets, your drivers, and your community safe. Don’t let your drivers skip this important step.
Your FMIS can make daily DVIRs more efficient and actionable. Use it to integrate daily inspections into your workflow.
Build your DVIR templates in your FMIS. Then set rules to send any issues to a queue where you can review them and determine whether to open a work order or add it to the next scheduled PM.
6. Track standard repair times (SRTs).
One of the best ways to improve shop productivity is by using your FMIS to track how long it takes to make specific types of repairs in your shop (i.e. standard repair times or SRTs).
SRTs are a key metric to benchmark technician efficiency from job to job. If you’ve never tracked this you can find industry benchmarks on ALLDATA or Mitchell 1, but these won’t take your fleet’s circumstances into account.
The best way to get SRT benchmarks is to have your mechanics start tracking repair times on every job. After you’ve accumulated several entries from multiple techs on the same type of repair, calculate the average time from your shop’s data and use that as your benchmark moving forward.
7. Plan the shop’s work.
If shop productivity is top of mind, let’s talk about proactive vs. reactive schedules. Proactive schedules are about planning the shop’s work in advance. They lead to:
- less stressful environments for techs
- higher employee and customer satisfaction
- better quality outcomes
- and reduce asset downtime
When work is planned, techs can be prepared to tackle repairs the moment the vehicle arrives so it can get back on the road as quickly as possible.
We recommend striving for at least 80% of the shop’s work to be planned. That may sound a little daunting but if you use your FMIS’s shop scheduling tools, it will make a night and day difference for your shop.
8. Automate warranty tracking.
Taking advantage of warranties basically equates to free parts and repairs. But who has time to check to see if every part or piece of equipment is under warranty?
Let your FMIS automate warranty tracking so you don’t leave money on the table. Most FMISs can notify you if a part or repair is covered under an OEM manufacturer’s or vendor’s warranty. They can also monitor your warranty claims to make sure you get reimbursement money back from your vendors.
9. Schedule preventive maintenance (PM) reminders.
Preventive maintenance is the key to keeping every asset in tip-top shape. You can have the best PM program in the industry, but if you don’t know when assets are due for PM checks, they won’t happen.
This is where your FMIS comes into play. All you have to do is set up a PM reminder schedule based on what “due soon” means to your operation.
First, set parameters for when you want to see PMs that are coming due. This could be 7 days in advance, 14, or even 30.
Second, make sure your FMIS notifies you when assets are coming due. At the very least, it should be able to email you a daily or weekly report. A modern FMIS will give you options to get automated text or push notifications. Remember to set additional alerts for due now and past due PMs.
With careful planning and a good alert system, you’ll have no problem staying on top of PMs, which will keep costs low and availability high.
Are You Getting the Most Out of Your FMIS?
Most FMISs are robust tools that have a wide range of capabilities. Likely, you’re not using them all.
If you want to get more out of your FMIS, we encourage you to take a step back and audit how you’re using your system. You can start by asking these questions:
- Who’s using the system? Who’s not?
- What data is going in? What reports are coming out? How is that data being visualized?
- Which features are you using? Which ones are you not using but should be?
If your team isn’t using the system, you can’t get the data you’re looking for, or it doesn’t have the features you need, it might be time to consider an upgrade.