Fleet Management Best Practices, Part 2: Vehicle Operation Management
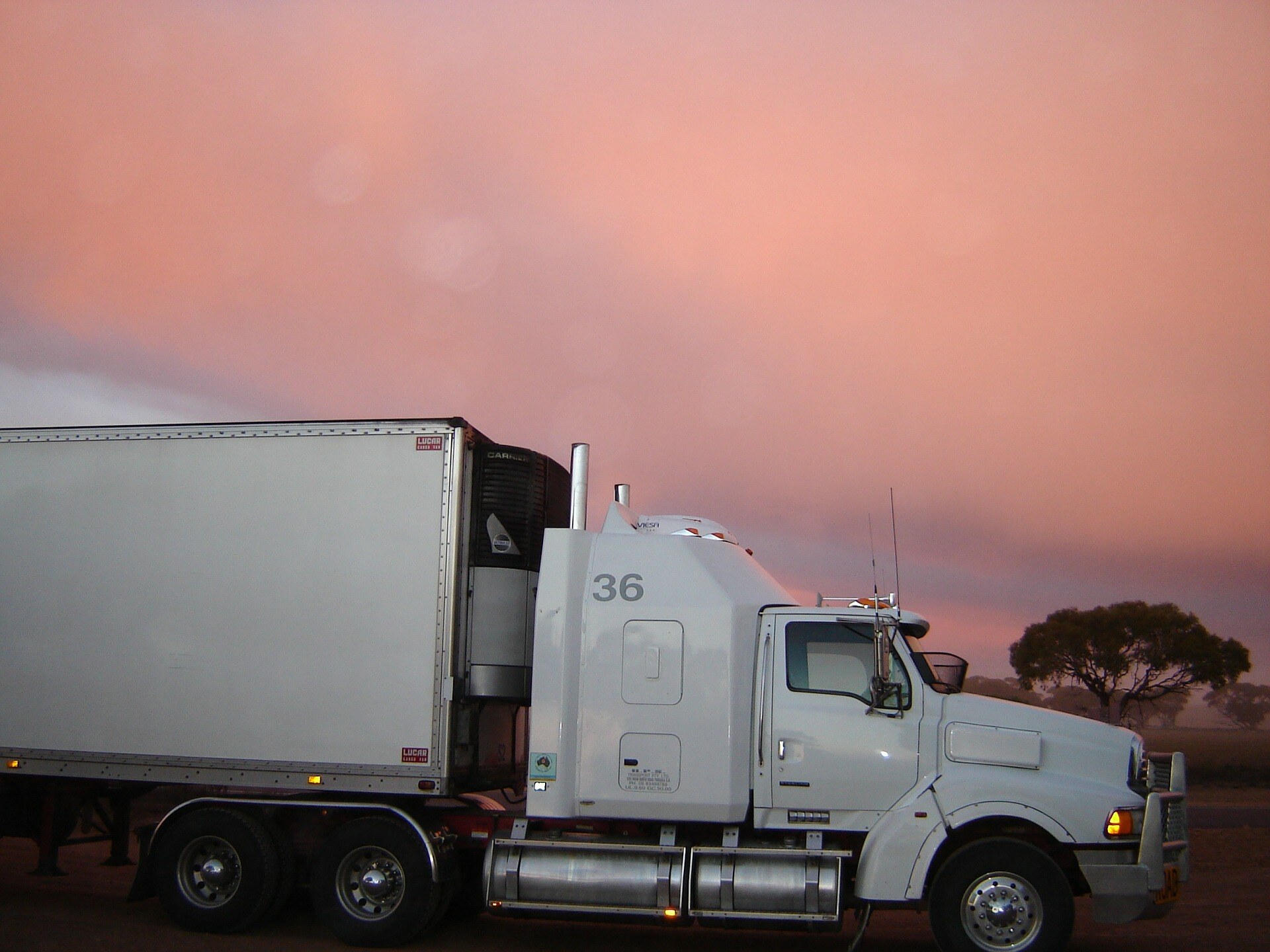
By Steve Saltzgiver, Fleet Success Ambassador
In Part 1 of this Fleet Management Best Practices series, we discussed the five key elements of vehicle acquisition and disposal. In Part 2, we will introduce you to the five elements of “vehicle operation management” which include the following best practices:
In this commentary, we will discuss each of these best practices in detail and describe what fleet management professionals must be looking to establish and implement in their respective organizations. These best practices should be the work product using a collaborative partnership between fleet management, its major peers (i.e., Risk, Finance, Human Resources, etc.), and a combination of small and large user departments. This partnership is generally referred to as Fleet Advisory Committee — allowing stakeholder feedback and buy-in to its policies.
OPERATOR CERTIFICATION AND RECORD KEEPING
Fleet management professionals have a fiduciary charge to ensure each driver possesses the proper credentials (i.e., vehicle type, age requirements, etc.) including licenses and endorsements to operate vehicles and equipment.
Operator policies and procedures must be present in the operation and enforced with disciplinary consequences for non-compliance. Operator procedures must include mechanisms to periodically review motor vehicle records (MVR) captured by government departments of motor vehicle (DMV) ensuring operator behavior is proactively monitored.
The mere physical possession of a driver’s license does not necessarily constitute whether it’s active or valid as drivers may possess their revoked license. These processes must be coordinated with the organization’s safety and risk management groups.
Moreover, if your organization operates commercial motor vehicles (CMV) there are many additional requirements that must be followed. As an example, driver records are required by the Department of Transportation (DOT) to document commercial driver license (CDL) validity, medical certification, endorsements like airbrake operations, hazardous material hauling, etc., drug clearinghouse information, and much more. Generally fleet management partners with its peer, Human Resources to track this sensitive personal data. Other DOT-related documentation includes completing the biennial MCS-150 form to register total CMVs and operators under the organization’s DOT number.
Further, organizations must have a reliable filing or record-keeping system, preferably an application (e.g., fleet management information system, etc.) to document and manage operator records in real time.
OPERATOR TRAINING
Many regard operator training as a core objective of non-fleet departments. However, operator (i.e., driver) training can really be a fleet manager’s best friend. Whether fleet management chooses to partner with external departments or develop its own operator training – it is essential to control expenses. Many progressive fleet management organizations offer formal new driver orientation or onboarding classes. Included in these fleet-initiated new driver onboarding sessions are topics such as:
- Fleet management policies and procedures
- Daily vehicle inspection reporting requirements
- Preventive Maintenance responsibilities
- Telematics data sources used to monitor driver attributes
- Required maintenance, care, and operation of assets
- Use of third-party maintenance services and supplies
- Equipment systems use and orientation
- Commercial vehicles use requirements
- Refusal to operate unsafe equipment
Operators are the eyes and ears of great fleet management. Thoroughly trained vehicle and equipment operators can aid fleet management in their charge to prevent unnecessary asset damage, breakdowns, road calls, and expenses.
PRE-TRIP INSPECTION AND RECORD KEEPING
Whether your organization operates a commercial fleet where a pre/post trip inspection is required by law, the fact of the matter is daily inspections are simply recognized as a fleet management best practice. An operator should never operate any piece of equipment until they know it’s safe to do so and have documented this inspection. Conducting daily vehicle inspections and proper record-keeping practices make sense to lessen the liability related to operating an unsafe asset.
This is best demonstrated by those accessing a vehicle from a rental company. Prior to renting, an operator is required to conduct a quick inspection of the vehicle’s condition. This inspection generally documents such items as minor body damage, tire tread depth, mirror, seat, and dash control operation, along with brake and steering functionality. As discussed above, this should be included in the new driver orientation program by fleet management.
VEHICLE MISUSE/ABUSE MANAGEMENT
The subject of vehicle misuse and abuse by drivers is often a very contentious and costly endeavor. One of a fleet manager’s biggest battles with vehicle operators is the reporting of asset misuse and abuse. When asked, generally no one takes accountability for this miscellaneous damage. The problem with driver misuse and abuse is the repair of these unplanned incidents really mounts up.
A well-designed cost charge-back program can aid in the mitigation of operator misuse and abuse by assessing this damage directly to the driver’s department. This cost charge-back program coupled with the operation of an Internal Service or Enterprise Fund, along with a detailed service level agreements (SLA), removes emotion involved in managing asset misuse and abuse.
Consequently, placing reporting accountability squarely on the asset users versus fleet management. It’s quite amazing how a policy this simple reduces these incidents as consumers make better fleet decisions when they incur the expenses.
Finally, the topic and examples of driver misuse and abuse must also be included in the organization’s fleet management orientation program. Moreover, familiarizing each operator with the proper use of each type of asset prior to deployment will prevent much of this misuse and abuse.
ACCIDENT REPORTING, INVESTIGATION, AND MANAGEMENT
Accident reporting, investigation, and management is generally a set of activities and policies managed by either the Safety or Risk Management department. However, because fleet management is involved in the accident repair process, they must become an integral partner with these other departments. Fleet can work closely with these agencies to provide a portal to track accident and repair expense data.
Additionally, the fleet can assist in the bidding, evaluating, contracting, and procurement of an external body repair vendor. Moreover, a best practice in fleet management is to directly manage or participate as a stakeholder on an Accident Review Committee (ARC). The ARC members assist in the accident root cause investigation and assessment to determine if preventable or non-preventable using National Safety Council Standards[1].
SUMMARY
Utilizing these known standards provides a greater level of consistency in the management of these tasks. An advanced organization utilizes these best practices to align expected driver attitudes and behavior with its goals. An example of a Best Management Practices Assessment can be found on the internet for the City of Exeter in the State of New Hampshire[2]. Moreover, there are many other studies and presentations available to illustrate these best fleet management practices[3]. The purpose of adhering to these known standards is to reduce costs, lessen confusion, align with organizational employee disciplinary policies and allowing stakeholders to have a voice in the policymaking and enforcement process.
The bottom line, there is no shortage of things that must be documented while managing and maintaining a fleet of assets. This article only touched on a few key processes related to operations management. It’s incumbent on each fleet management organization to ensure they are dotting the “I’s” and crossing the “T’s” to remain in compliance with the myriad industry regulations.
[2]https://www.exeternh.gov/sites/default/files/fileattachments/public_works/page/4441/fleet_study_2009.pdf
[3] https://mercury-assoc.com/wp-content/uploads/Fundamentals_Of_Fleet-Management-How_Telematics_Solutions_Providers_Can_Help_Their_Customers_Be_Better_Fleet_Managers-BUDAPEST_SEPT-2016.pdf