Shop Management: How to Run Your Fleet Shop More Efficiently
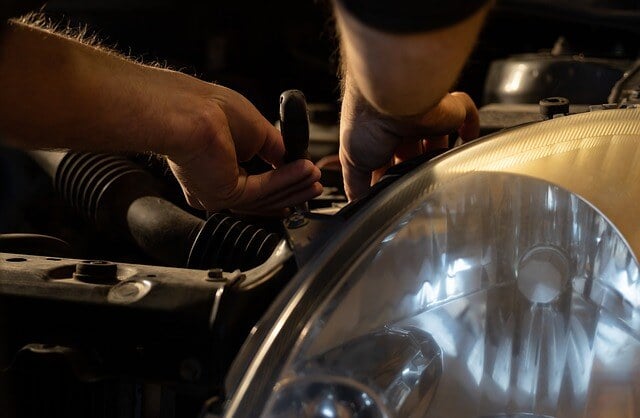
By Mary Gerard, Content Marketing Manager
Owning, operating, and maintaining a fleet today is extremely complicated. And let’s be honest – very stressful.
The hours are long, and the list of responsibilities is even longer.
You must function on a tight budget and perform the same amount of work (or more) with a reduced staff. You’ve been struggling to retain and recruit technicians, and now you’re losing some of your most skilled ones to retirement without a group of replacements walking in the door.
We could go on and on, but you are all too familiar with your list of challenges.
So, let’s focus on some ways to make your life as a fleet professional better.
Track Work Orders
How much work is coming into your shop? What type of work are your technicians doing? How many open work orders do you have? On average, how long does it take to complete a work order? How long are your vehicles out of service for repairs?
These, and others, are all questions you should be able to answer on the spot to ensure your shop is running efficiently. Here are some helpful hints:
Use an FMIS: One of the best ways to track the work in your shop is to use a dedicated fleet management information system (FMIS). These software solutions can be one of the best tools that a fleet manager has in their toolbox. The right system will allow you to track work on the shop floor with a robust work order management module, schedule work into the shop, track technician productivity, allow for predictive analysis, identify common issues with specific assets, parts, or vendors, and report on fleet performance.
Create a Preventative Maintenance (PM) Program: A good PM program is fundamental to keeping your fleet on the road and out of the shop. A PM program provides for systematic inspection and replacement of critical fluids and other components and allows your technicians to identify potential issues before they become a larger and more costly problem. Using an FMIS, you can set PM intervals (i.e., every 7,500 miles), PM levels (i.e., PM-A Service), and schedule the services in advance. Scheduling PMs in advance gives your staff time to build parts kits and make sure that they have the necessary parts, fluids, and more, on hand when the vehicle arrives at the shop. You can also monitor PM compliance (Are the drivers bringing their vehicles in when they are due for a PM?) and more importantly, compare scheduled work (i.e., PM services) versus unscheduled repairs, which is a key fleet performance metric. Ideally, the majority of the work in your shop will be of the PM variety.
Link Work Orders to Vehicles: Using an FMIS, you will be able to track asset-level maintenance and repair history to specific vehicles and to technicians. The benefits of this level of maintenance and repair data are huge. Not only will this enable your organization to track total cost of ownership, but you will also be able to track warranty claims for parts and labor.
Assign WOs to Technicians: Work should be assigned to technicians based on skill set and availability. By using an FMIS, you can monitor technician workload, efficiency, and effectiveness. It is a useful tool to review task level accomplishments and to identify potential areas of additional training.
Track Costs Linked to WO: The FMIS will allow you to track all costs associated with the repair or preventive maintenance services. This includes the labor, cost of parts, and expenses for outside vendors used to complete the work. Monitoring these expenses lets you track the total cost of repairs for the asset, which can help with your budget, calculate total cost of ownership, and to start using data to make informed decisions such as when should we replace this vehicle.
Manage Parts Inventory
Since parts costs account for up to about 30 percent of your fleet maintenance and repair expenses, your inventory should be actively managed. An FMIS will help you manage your in-stock inventory levels, notify you when to re-order parts using min/max levels, identify obsolete parts that have not been used, and ensure that you are not experiencing any parts shrinkage (theft).
Monitor Your Data
To improve your shop management, you need to know what’s going on in crucial areas, always. You can accomplish this through data. With an FMIS, you can pull analytics and monitor key metrics to look for issues in your fleet, or to see what’s going well.
Some data you should monitor in your shop include:
Fuel usage: Fuel is one of your fleet operation’s largest expenses. It’s important to track how much fuel each vehicle is using. This will help you better account for fuel costs and to identify any anomalies. Monitoring your fuel usage will also identify any drivers that are wasting fuel through bad driving behaviors like idling, or even for personal use of the vehicle.
Work orders: It’s important to track the number of open work orders, closed WOs, and the average amount of time to complete a WO. This can help you monitor the productivity of your shop and can identify any training or performance issues with your technicians.
Meter readings: Tracking each vehicle’s utilization (miles driven or hours operated) can help you determine if the asset needs PM services, how much fuel it is using per mile/hour, and if the driver is keeping the vehicle on the assigned route.
Vehicle usage: It’s essential to monitor how often each asset in your fleet is being used. If your fleet has several vehicles with low utilization, this may be a sign that there are too many vehicles in the fleet.
Total cost of ownership: Tracking how much it costs to keep a vehicle in your fleet is important. This includes not just the purchase price of a vehicle, but also operating and maintenance expenses. Knowing this information can help you determine when an asset should be replaced.
Direct labor: How much time are your technicians actually spending on jobs (wrenching time)? This is important to document as part of shop management so you can track your labor costs and note how much time is spent directly repairing vehicles. Conversely, tracking indirect time spent on non-wrenching tasks is important because it can help determine if you are employing the correct skillsets. For example, if your technicians are routinely exceeding standard productivity goals (i.e., direct labor hours per year), then you may have justification to add more technicians. Conversely, if you are paying skilled technicians to perform non-essential shop functions then maybe a lesser skilled employee should be hired so the technicians can focus their efforts on vehicle maintenance and repair activities. A good industry benchmark for direct labor is between 65 and 75 percent for wrenching technicians.
Standard Repair Times (SRT): How long are your work orders taking to close out versus the industry standard for how long a particular job should take to complete? Track your technicians’ completion times against industry standard times or internal times to see if your staff is taking longer than average to finish repair jobs.
SRTs are used to gauge individual technician productivity compared to their peers and others in the industry. Each original equipment manufacturer (OEM) sets SRTs for all diagnostic time, component replacements, preventive (routine) maintenance and warranty repairs. Using SRTs allows management to determine how skilled each technician is relative to each asset’s mechanical systems. As an example, fleet shops expect an average technician to perform within 90 to 100 percent of the set SRTs. A high-performing employee may exceed 110 percent. SRT information can be critical to determining the type of training employees may need within the fleet operation. It can also help you make better staffing decisions, ensuring the right number of technicians are available in an ever-shrinking skilled labor pool.
Improve Technician Productivity Through Shop Management Tips
Tracking SRTs is a great way to track how much time your technicians are spending on each job. This will go a long way in making them more efficient. In addition to getting them close to SRTs on work orders, there are other ways you can improve your technicians’ productivity.
Guiding them to perform more efficient inspections can reduce the time it takes them to perform PM. Using what RTA’s founder Ron Turley called The Circle Method, you can diagram a vehicle and break it into small areas. The idea is the technician needs to inspect each element of the vehicle within that area before moving onto the next “circle.” This prevents technicians from back tracking, rechecking the same areas and wasting time.
Another tip is to watch how your technicians work. Are they constantly leaving the vehicle to get a tool or a part? How far are they walking to get an air hose? Moving items around your shop or putting processes in place to get all parts before you start working on the vehicle, or gathering tools, can help save time.
Listen: Technician Productivity
Keep Your Fleet Compliant
Part of managing your shop is keeping vital information on-hand and updated. If you are subject to internal or external audits or must provide information to the Department of Transportation, you don’t want to get caught without the records you need.
Provide maintenance reports: The DOT requires operations to show a vehicle’s maintenance records to an inspector to prove needed repairs have been made. A fleet management information system can store work orders and vehicle records in the system, making them easily accessible.
Perform vehicle inspections: The DOT requires drivers to conduct pre- and post-trip inspections on commercial vehicles. These inspections need to be kept on file for three months to demonstrate any defects and prove they were repaired. When an electronic DVIR syncs with an operation’s FMIS, the defects and repairs can be added to the vehicle’s records, and the inspection reports are kept within the solution. This makes it easy to show inspectors the notes and any repairs that were required.
Keep Records of Accidents: Fleet operations need to keep reports of any recordable accidents. This can be easily added and stored in the FMIS. Instead of having to keep track of paper forms, operations can quickly access the records through the software system.
Efficiency Is Possible With Shop Management
When you’re running a shop, you have a lot of responsibilities each day. It’s essential to add efficiencies where you can to get through your to-do list and most importantly – keep your vehicles safe and on the road.
Fortunately, there are solutions. One of the best ways to add efficiency to your shop is through fleet management software. The right FMIS can help you organize your work orders, track cost and maintenance and repair activities, report on fleet performance and keep your shop and vehicles compliant.
To learn how RTA’s fleet management software solution can help your fleet operation, schedule a free demo today! If you need help improving your shop operations, right sizing your fleet, developing fleet renewal plans, identifying opportunities for improvement in your fleet operation, etc., contact one of our professional fleet consultants.