Why Your Fleet Needs an Organized Preventative Maintenance Program
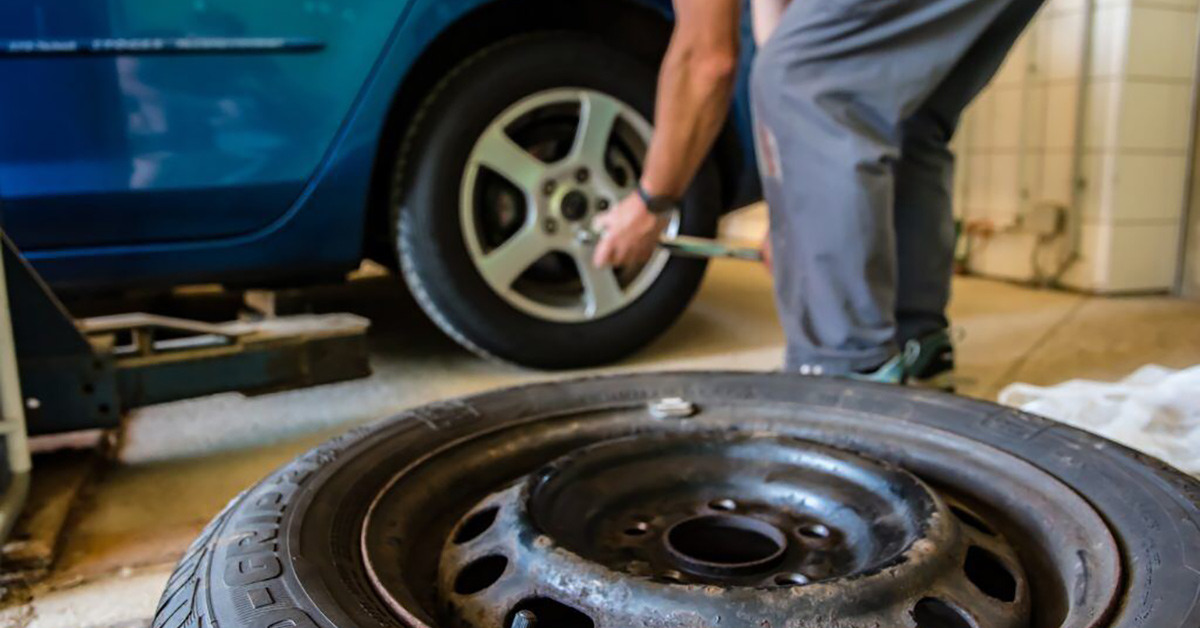
The key to any fleet operation’s success is keeping its vehicles on the roadways. This requires avoiding unplanned breakdowns and large repairs on assets — which can be four times more costly. One way to ensure these vehicles are properly maintained is to create an organized preventative maintenance (PM) program at your fleet operation.
Preventative maintenance is the routine services of vehicles to inspect them at regular intervals and perform small services regularly — like oil changes and fluid refills — to keep an asset in good operating condition, and hopefully prevent larger problems later. Performing PM services can also help keep your fleet compliant with Federal Motor Carrier Safety Administration (FMCSA) mandates to ensure your fleet operation is safe and efficient.
Unplanned breakdowns and large repairs on assets can be four times more costly than scheduled services.
To make your PM program successful, it’s important to invest time planning the program and properly scheduling assets for services in accordance with manufacturer guidelines.
First, it’s essential to understand why your fleet operation needs an organized PM program. In this white paper we will outline how a properly run PM program can help reduce unexpected repairs, decrease operating costs, prolong the lifespan of the assets, and help your operation better track part warranties.
REDUCE UNEXPECTED REPAIRS
At the heart of a preventative maintenance program is the goal of reducing unexpected repairs. In a functioning PM program, small issues are caught during pre-scheduled maintenance services that help reduce larger issues later and prevent unplanned repairs. The goal is to make the majority of your shop’s work orders focused on preventative maintenance instead of demand maintenance.
PM vs Demand Maintenance
Preventative maintenance refers to servicing a vehicle regularly to complete an inspection and perform routine services to keep it running properly and efficiently. If any defects are found during PM, replacement and repair services will be either performed during the service (if time and parts are available) or work orders will be created for the minor work to be completed later.
Some typical tasks performed during PM services can include:
- Oil change
- Air filter change
- Lube application, if needed
- Belts and hoses inspection and replacement, if needed.
- Engine air filter inspection and replacement, if needed.
- Cabin filter replacement, if needed.
- Check transmission fluids and replace, as necessary.
- Check windshield washer fluid and refill as needed.
- Replace the fuel filter as needed.
- Check the power steering fluid and refill as needed.
- Check and refill the coolant, as needed.
- Test the battery and its connections and replace as needed.
- Check the timing belt and replace as needed.
- Perform a tune-up and inspect the spark plugs.
- Check the entire brake system and replace brake fluid as needed.
In contrast, demand maintenance refers to unscheduled maintenance. This is only performed when a vehicle encounters a previously undetected defect or unexpectedly breaks down. Demand maintenance can put stress on your parts room and shop as parts need to be located – and possibly ordered – and technicians may need to work overtime to complete the unexpected repairs. This can have a downward effect on other previously scheduled repairs and can negatively impact your operation’s maintenance budget.
DECREASE OPERATING COSTS
Preventative maintenance programs do more than help keep your vehicles on the roadways – they can also save you money on operating costs. An organized PM program can reduce labor, maintain compliance with Manufacturer warranty, decrease the amount of extra and last-minute parts being ordered, and minimize the number of large, expensive parts needed.
Reduce labor: According to RTA’s founder, Ron Turley, 1 hour of preventative maintenance can save operations 3 to 8 hours of labor. This is partially because when vehicles receive regular PM, the service requests are smaller and take less effort to repair. Large, unexpected fixes can require more labor hours and possibly even overtime so technicians can get the vehicle back on the roadways. Unplanned maintenance can also result in wasted labor on driver hours if he or she is sitting around the shop waiting for the vehicle to get repaired.
Save money on parts: Demand maintenance can leave your technicians without the parts they need to perform repairs. With preventative maintenance, you know when vehicles are due for specific services, allowing your shop to stock the right number of needed parts – including materials to change the oil and other routine services. If defects are found, PM also gives your shop ample time to order parts to make smaller repairs.
Avoid costs from tows and road calls: PM is meant to help prevent vehicle breakdowns. This can help your operation save money on towing vehicles into the shop or making road calls.
PROLONG VEHICLE LIFE EXPECTANCY
An organized preventative maintenance program can help prolong the lifespan of your fleet vehicles. These PM services can do the following:
Keep vehicles well-maintained: Scheduling regular preventative maintenance services can provide assets with needed oil changes, lube applications, fluid refills, battery tests, spark plug replacements, and other routine services that keep the vehicles running efficiently and help reduce wear and tear.
Control rust and corrosion: Regular PM services give technicians the ability to treat rust and corrosion as it occurs, extending the life of the asset.
Inspect lines and hoses: Technicians can check and replace lines and hoses throughout the vehicle during preventative maintenance services. This can help prevent these parts from completely failing – possibly causing serious issues like engine damage.
GAIN MONEY IN PARTS WARRANTY CLAIMS
An organized preventative maintenance program can allow technicians to take the time to inspect parts that are currently under warranty and look for signs of wear and tear. If the parts need to be replaced, a regular PM schedule will let technicians install new parts while they are still under warranty, giving money back to the operation.
Dedicating the time to check for under-warranty parts during PM and developing an organized warranty program can be worth the investment for your operation. According to Ron Turley, 5 minutes of paperwork can yield $110 of warranty.
5 minutes of paperwork can yield $110 of warranty.
While your fleet operation might be focused on inspecting the large parts during PM that can be replaced under warranty, it’s important to inspect the small parts as well. Claiming warranties on small parts can generate needed money for your operation, and ignoring these warranty claims can cost your operation tens of thousands of dollars in part replacement expenses.
To ensure these warranty claims don’t fall through the cracks, operations can use their fleet management software system to track the warranty information for each part, and then have the parts inspected during regular PM services.
SAVE TIME ON INSPECTIONS
Part of an organized preventative maintenance plan also includes instructions for how technicians should perform PM services. Conducting PM inspections in the right order can save techs time.
According to Ron Turley, preventative maintenance is done in the right order if a technician does everything he or she can from one spot before moving on to the next area, and if a tech does not have to retrace his or her steps during the inspection.
Using a circle method can help technicians avoid wasting time during a PM inspection. Ron Turley believed that everything a tech needs to inspect should be within a 3-foot circle. This means that technicians should break the vehicle into manageable 3-foot sections during their inspection, so they can focus on one segment of the asset at a time – without rechecking the same area of the vehicle.
Turley recommended technicians start by sketching the vehicle and then drawing circles around it that represent about 3-foot areas in diameter. The circles should overlap slightly to ensure every part of the vehicle is examined. A systematic structured approach to performing each inspection task ensures nothing critical is overlooked.
Once the diagram is set, the technician can design a task list based on manufacturer recommendations and start inspecting the asset.
CONCLUSION
Creating an organized preventative maintenance program at your fleet operation can have several benefits. While the main advantage is preventing unplanned breakdowns and large, unexpected repairs in your fleet vehicles, other benefits can include decreasing operating costs, prolonging the life expectancy of your assets, gaining money on parts warranty claims and saving time on vehicle inspections. Finally, and most importantly a structure PM program ensures assets are maintained safely in a roadworthy condition to protect the driver and the public at large.