Making Drivers More Efficient, Accurate at Vehicle Inspections
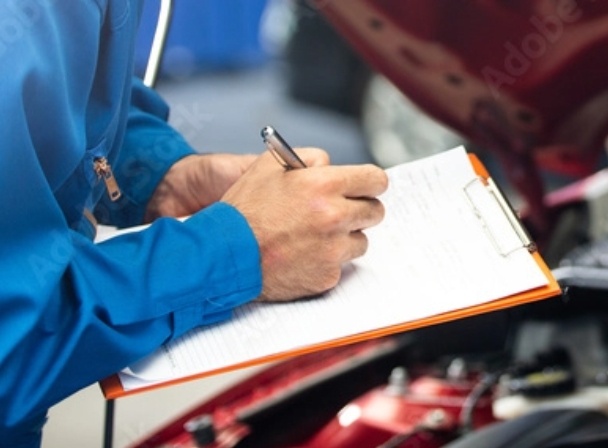
The Department of Transportation requires fleet drivers to complete pre-trip inspections on vehicles before beginning their routes. How drivers perform these examinations can vary.
While some drivers might skim through the inspections – leaving themselves and others on the roadways at risk – some might spend too much time conducting them by following an inefficient process.
To improve vehicle inspections, fleet drivers must have a comprehensive inspection form, know how to perform an inspection efficiently and accurately, and identify what tools can best help them complete reports.
Use Customized Inspection Forms
Stop wasting time on generic inspection forms and create checklists that are customized to the specific vehicle the driver is operating.
Have a Plan for How to Complete Inspections
Reduce the amount of time spent on inspections by following a plan for how to inspect the vehicle without checking the same areas over and over again.
Stop Using Paper Forms
Using paper forms can limit the notes drivers can record, cost technicians extra time to decipher the drivers’ handwriting, and increase the risk of losing the report.
Start Using eDVIR Solutions
EDVIR solutions allow you to create detailed reports, upload images of defects, communicate with the shop and keep the vehicle’s information in one place.
USE ACCURATE INSPECTION FORMS
Fleet drivers can be slowed during an inspection if they are using a generic form that forces them to skim over sections that do not apply to their vehicle.
When drivers conduct vehicle inspections, they should use a form that both adheres to the Department of Transportation1 requirements and is customized to the vehicle they are operating.
The DOT mandates that drivers inspect the following items:
- Service brakes, including trailer brake connections
- Parking brake
- Steering mechanism
- Lighting devices and reflectors
- Tires
- Tires
- Windshield wipers
- Rear vision mirrors
- Coupling devices
- Wheels and rims
- Emergency equipment
In addition to these basic elements, forms can be customized per fleet vehicle to account for specific systems. For example, a school bus or police vehicle will have different safety elements to inspect than a passenger van. These unique features can be accounted for in a customized form.
Forms can also be created to adhere to a fleet operation’s own safety requirements and inspection protocols.
CREATE AN INSPECTION PLAN
If fleet drivers are spending either too little or too much time performing vehicle inspections, fleet managers and supervisors can help identify areas where drivers can improve their processes.
When observing drivers complete inspections, managers should pay attention to:
How many times drivers pass by the same area of the vehicle: If drivers repeatedly pass by the same parts of the vehicle during an inspection, they are wasting time. To prevent this, managers should observe drivers performing a routine inspection.2 On a piece of paper, he or she should draw a rectangle in the center. The manager should mark where the driver moves around the vehicle and put an “X” where he or she stops to inspect the asset. When the inspection is complete, he or she can note how many areas have a double “X.” The manager should share the results with the driver and discuss how he or she can be more efficient during an inspection by avoiding looking at the same areas of the vehicle multiple times.
What slows drivers down: While observing drivers perform a vehicle inspection, managers should also make note of anything that slowed down his or her process. This can include if the form was too cumbersome, if the driver spent too much time adding detailed notes, or if the form was not specific to the vehicle they were inspecting. Making note of these items can help managers determine if their operation needs to create better inspection forms and if it needs an Electronic Driver Vehicle Inspection Report (eDVIR) application to help drivers quickly and accurately perform inspections.
STOP USING PAPER FORMS
While drivers can accurately perform inspections on paper forms, these sheets can have some negative effects for drivers and the shop’s technicians:
Take too long to complete: Paper forms require drivers to complete inspection notes by hand. These can take longer to complete as drivers try to make their handwriting legible so the technicians can decipher their notes.
Do not provide enough detail: Drivers are limited by space available on the form when trying to give a detailed description of a vehicle defect. This can result in incomplete notes, which can cause a communication gap between the driver and technicians.
Are not customizable: Paper forms might not be customizable, leaving drivers to sort through sections that do not relate to the vehicle they are inspecting. They can also fail to include special systems on a vehicle, leaving a gap in the inspection.
Are easy to misplace: To abide by DOT mandates3, inspection reports need to be kept on file for three months. The paper form must make it from the driver to the shop without getting misplaced before it is filed.
Must be hand-delivered: Paper forms need to be brought into the shop and given to the technicians. This means the shop cannot start preparing for the repairs until the driver brings the inspection report to the technicians.
START USING EDVIRS
Instead of using paper forms, fleet operations can improve the accuracy and efficiency of vehicle inspections with eDVIRs. Some of the benefits these applications can provide to operations include:
Easy-to-read notes: Instead of trying to scribble notes quickly on a paper form, drivers can use the eDVIR app to accurately type notes into the form. This makes the reports easy for technicians to read. Some apps, like RTA Inspect, also let drivers use their voice to leave detailed notes.
Add images: eDVIRs can also provide drivers with the option of uploading images of defects into the app. Instead of a driver trying to explain the defect, he or she can take a photo of it and share it with the technicians in the inspection report.
Customizable forms: eDVIR apps allow operations to easily customize inspection forms. This makes the forms more efficient – and accurate – for drivers to complete.
Store all files in one place: eDVIR apps can sync with fleet operations’ fleet management software systems. This allows fleets to store a vehicle’s information in one safe, secure place.
Improve communication between drivers and technicians: When using an eDVIR, drivers can save the inspection in the app – making it easily accessible by the shop. This eliminates the need for drivers to hand-deliver paper forms. The technicians can see the drivers’ notes before the vehicle even arrives in the shop and can prepare for the repairs.
CONCLUSION
Don’t let fleet drivers waste time – and risk their safety – with inaccurate and inefficient vehicle inspections. Instead, make sure they are using complete inspection forms, and that they are inspecting the vehicle in the most efficient manner.
Fleet operations that use paper forms can also consider switching to an eDVIR application to improve the communication between drivers and technicians, provide customized inspection forms, allow drivers to upload images of defects, and store all of the information in one secure and accessible location.
According to the FMCSA, drivers spend a combined 46.7 million hours each year completing DVIRs. Save your fleet operation time – and money – by using eDVIRs to make drivers’ inspections more efficient.
Resources
1 https://www.fmcsa.dot.gov/safety/passenger-safety/inspection-repair-and-maintenance-motor-carriers-passengers-part-396
2 RTA Fleet Management Software Tip Sheet: Vehicle Inspections
3 https://csa.fmcsa.dot.gov/safetyplanner/MyFiles/SubSections.aspx?ch=22&sec=65&sub=148