4 Best Practices for Your Parts Management Program
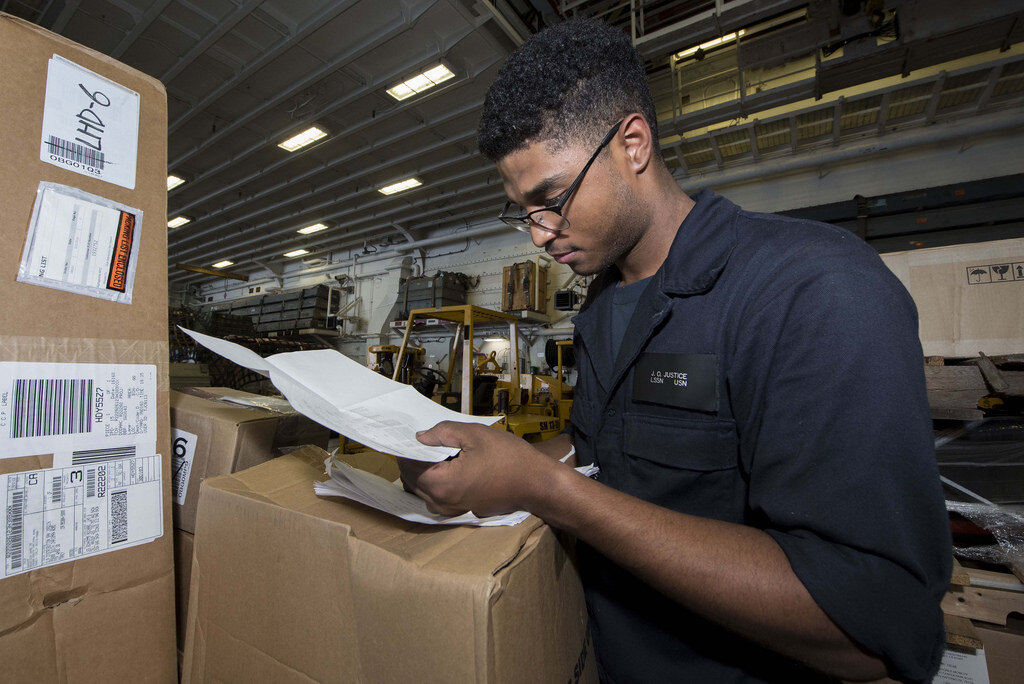
Proper parts management is critical for fleet operations. When parts need to be replaced, spares need to be available -- but keeping too many spare parts can increase inventory and costs.
Running an efficient parts management program requires the knowledge to know what’s the magic number of parts to keep in your inventory. Determining this can be done through classification of inventory, forecasting, preventative maintenance and installing fleet management software.
Determine a Classification System for Your Inventory
Your fleet’s inventory should be prioritized when determining the amount of spare parts that should be kept on-hand. This will help you identify the frequency specific parts should be restocked. One method is the ABC model. This will help you classify the most critical assets.
- A: This should be assigned to the most important parts -- the ones that require you to monitor their inventory the most. The “A” group should account for 20 percent of your total inventory. Because this group is used the most, it’s crucial to have these parts on-hand.
- B: This group is less important than the “A” group, but it’s still important to monitor its inventory closely. This group should make up 30 percent of all inventory.
- C: This is the least important group. This group should make up 50 percent of your overall inventory.
Other classification methods can also be used. The important step is selecting a method that helps you classify your inventory in a way that’s most useful to your operation.
Use Forecasting and Reporting
It’s important to know how your operation typically uses certain parts when determining how to manage your spare parts inventory.
Looking at your fleet’s reports and historical data can help provide the needed inventory information. Tracking how long parts typically last, which brand has the best performance, and how often parts require maintenance can be useful when deciding how often to restock your inventory.
Reports can also be used to determine the downtime a piece of equipment would endure if a particular part was out of stock and needed to be reordered. This can alert you to how many spares you should keep on-hand. If you do need to restock a part, knowing its importance can also help you decide which parts should be sent via expedited delivery and which can wait for standard delivery services.
Perform Regular Preventative Maintenance
Scheduling your equipment for regular preventative maintenance can reveal the condition of parts. This will help you identify parts that will need to be replaced soon, giving you time to make sure the part is in-stock, or order a new one if needed. Parts can also be repaired – or scheduled for further service appointments – during preventative maintenance.
Install Fleet Management Software
Using fleet management software can help streamline your parts management program. Software, like RTA’s solution, allows you to easily set up a parts management system, allowing you to access your parts inventory, pull reports, view historical data, track warranties, schedule preventative maintenance and create work orders. Having all of the information in one place allows you and your staff to access information in real-time and simplify the process.