You Don’t Need Luck with an Organized Preventative Maintenance Program
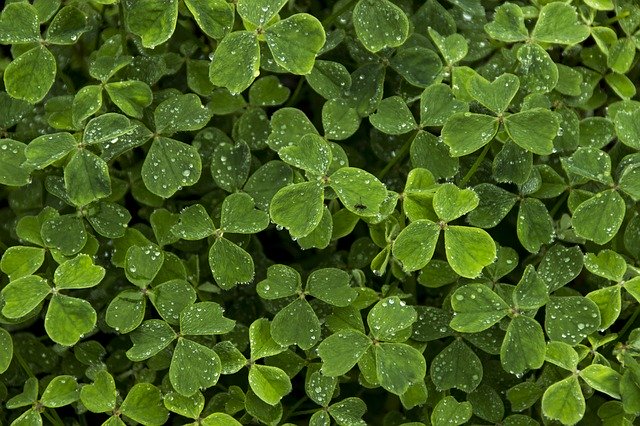
We’ve all seen it before – a fleet vehicle broken down on the side of the road. While our instinct might be to think what unfortunate luck for the driver and the fleet operation, there is a way to avoid these break downs without needing luck – preventative maintenance.
An organized PM program can help fleets identify potential problems early and try to avoid major repairs later that can lead to break downs and downtime.
Find out how a preventative maintenance program can benefit your fleet operation.
Track Individual Vehicles
Preventative maintenance programs allow your fleet operation to monitor individual vehicles on a regular basis. This enables technicians to check assets for issues and perform routine maintenance, such as:
- Wear and tear: Technicians can document any issues and replace components as needed.
- Check fluids: During PM, all the vehicle’s fluids should be checked and refilled as needed. Technicians should also check for any leaks during these inspections.
- Check tires: Technicians should check the vehicle’s tires to ensure they are at the right pressure and to make sure the tread is at a safe level. Tire rotations can also be performed.
- Change the oil: Part of a routine preventative maintenance check should include changing the oil according to the vehicle’s manufacturer guidelines.
- Odometer readings: Technicians can document the odometer reading to ensure the vehicle’s information is updated and to track fuel usage and schedule future PM.
- Warranties: Operations can monitor if the vehicle or its parts have any warranties expiring soon. Those components should be checked to determine if they are working or if a warranty claim needs to be filed.
Proactive Work vs Reactive
Preventative maintenance programs allow fleet operations to focus on proactive work versus reactive. During PM, technicians can inspect vehicles and identify small issues that could potentially turn into larger problems later. This allows them to proactively repair the vehicle.
In reactive work, fleet operations repair a vehicle after it has broken down. This can cause an increase in labor as employees are scrambling to repair the vehicle and find the needed parts. It can also cause drivers to change routes and schedules to adjust for the broke down vehicle.
Reduce Downtime
Preventative maintenance programs can allow fleet operations to reduce vehicle downtime by inspecting vehicles on a regular basis for issues. This lets assets get repaired during PM instead of being sidelined later for larger repairs.