10 Must-Know Tips for Your Parts Room Staff
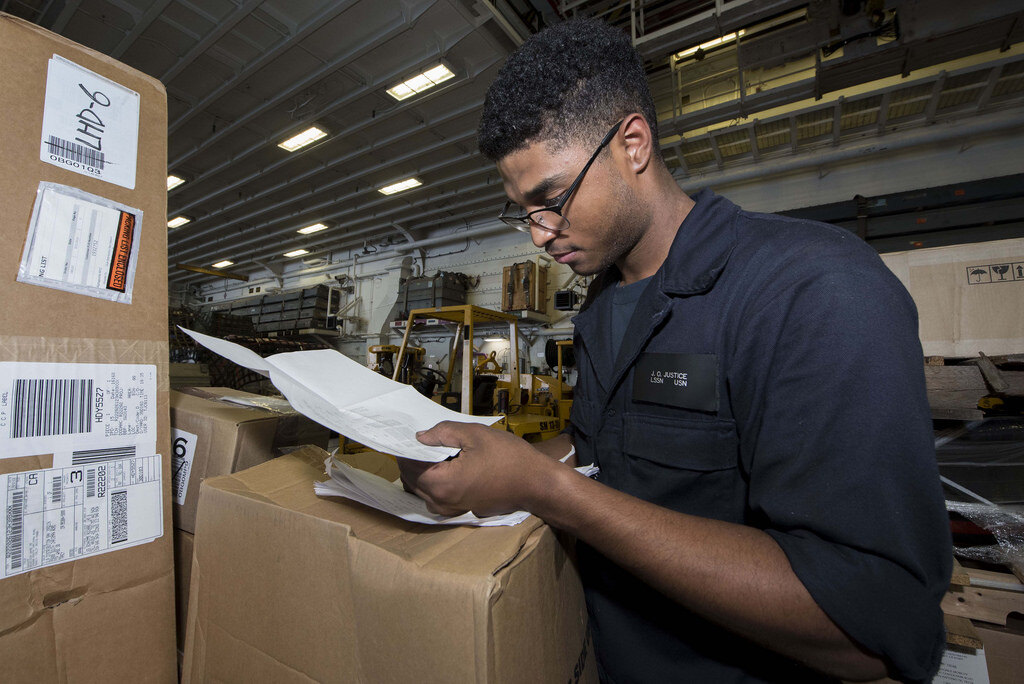
“All great changes are preceded by chaos,” Deepak Chopra.
The parts room is a vital component of your fleet operation. You need to keep the right parts on the shelves, and you must know where they are – quickly. With more and more pressure on fleet operations to operate efficiently, it’s essential to trim time where you can. This makes it essential to have a dedicated parts room staff you can rely on to quickly locate parts when needed to complete jobs, reorder parts in a timely fashion, and establish a good relationship with suppliers to get the parts you need at a good price and when you need them.
To accomplish this, your parts room staff needs to be informed. Make sure they know these important tips.
Organize and Label the Parts
Your parts room should be well-organized. This can be accomplished by assigning specific locations for each part type and labeling shelves, bins, or drawers. Doing this will streamline parts inventory management processes and make it easier – and faster – to locate parts.
Use an FMIS
It’s crucial to correctly and efficiently track your parts inventory. Using fleet management software can help. An FMIS lets fleets track parts, monitor stock levels, and automate reordering processes. This ensures efficient inventory control and reduces the chances of running out of key parts or over-ordering others.
Conduct Regular Audits
Perform routine audits to verify the accuracy of your inventory. Regularly compare physical stock counts with recorded quantities to identify any discrepancies or potential issues, such as missing or damaged parts. This will also help identify slow-moving parts that are taking up space on shelves.
Establish Reorder Points
To ensure fleets don’t run out of parts, it’s important to determine minimum stock levels for each part and set them in the FMIS. When the stock reaches or falls below that level, it will trigger an automatic reorder, ensuring that you have the needed parts in stock.
Properly Train Parts Staff
It’s crucial to train your parts room staff on how to take inventory, organize parts, reorder items, work with vendors and other tasks. This will keep your parts room running smoothly and will ensure you have the right parts on your shelves when you need them.
Consider a First-In, First-Out (FIFO) Strategy
To keep older parts moving off shelves, fleets should consider a FIFO strategy. This is where the oldest parts are used first. This prevents stocking older or obsolete parts or keeping expired or outdated parts on the shelves.
Secure the Parts Room
At one time or another, every fleet operation has had parts disappear out of inventory. Whether we want to believe it or not, employees can walk off with parts. To avoid this, access should be restricted to just the parts room staff. This will help reduce theft.
Keep Supplier Information on File
It’s crucial for the parts room staff to develop close relationships with vendors, and to keep all of their information in a central location. This should include keeping parts descriptions, purchase records, pricing, and vendor contacts on file.
Continuously Evaluate Process
Keeping a parts room running smoothly is an ongoing project. Fleet operations should continuously review the process and make changes as needed to provide improvements to make it more efficient.
RTA’s parts inventory solution is the best in the industry. Learn why when you schedule a free demo!