10 Tips for How to Organize Your Fleet Operation’s Parts Room
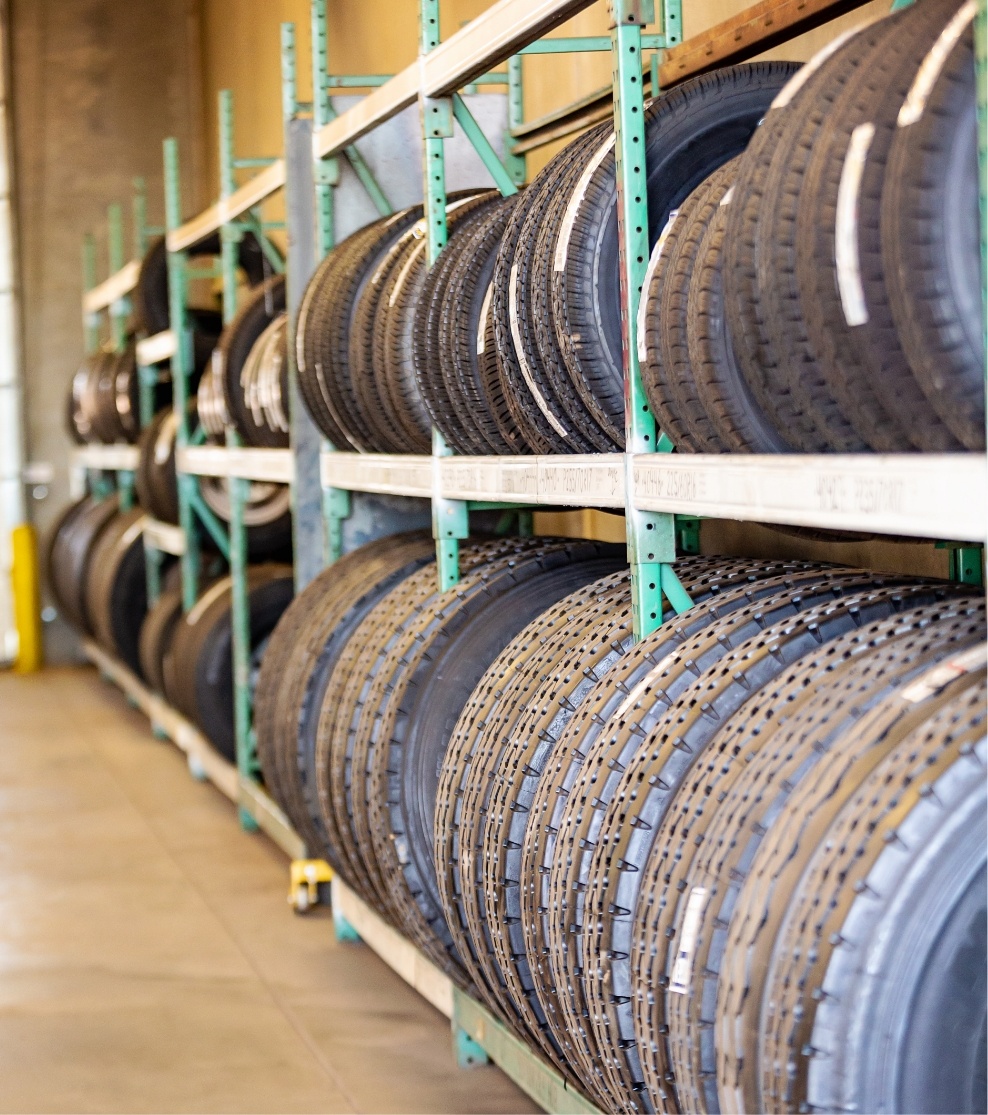
Parts rooms can quickly become one of the most disorganized areas of a fleet operation. Without order and planning, technicians and other staff members can waste valuable time trying to track down parts to complete tasks, and parts can be over-ordered if inventory isn’t updated, costing operations money.
To prevent this, fleet operations should organize their parts room in a way that’s conducive to their shop. Get tips below on how operations can consider organizing their parts rooms.
Assign Staff to Parts Rooms
Parts rooms should have designated staff members to work them. Employees should have specific responsibilities to ensure the parts are properly organized, stocked, and ordered. This can include hiring a Parts Room Manager, Parts Clerk, and other staff.
Keep Parts off of the Floor, Aisles, or Walkways
For both safety and organizational purposes, parts should not be stored on the floor or in areas where staff members walk. This will help prevent staff members from tripping over parts. It will also help all employees better locate parts if they are organized and stored on shelves and in bins.
Store Parts in Boxes/Bins
Instead of storing parts on shelves separately, place parts in boxes and bins and keep shelves organized. Single parts are more likely to get lost or combined with other types of parts. Keeping items in boxes and bins will help parts be easily grouped and quickly located. Operations can choose how to organize the bins, if they want to group by part type (for example, engine parts), or by manufacturer, or another convention that works best for their day-to-day needs. Bin locations should be labeled to identify the row, section and shelf they are located on.
Label Rows, Shelves, Bins
To help parts shop staff members quickly locate parts, all rows, shelves and bins should be labeled with an organizing structure. A potential structure could use the following: letter for row, numbers for shelving section, shelf number and bin number. For example, A5-3B4 would be located in row A, on the fifth shelving section, on the third shelf, in bin 4.
An example can be labeling all rows with letters and shelves with numbers, so a part could be located at A1, letting all employees know exactly where each part is located. This will help employees easily find parts, as well as quickly return them to the correct place.
Designate a Special-Order Shelf
To keep special-ordered parts easily identifiable – and to ensure they are not mistakenly used on another job — a shelf should be designated and labeled specially for them. This shelf can have special markings or colors, too, to ensure it is clear it’s for special orders only. Parts can also be tagged with a twist tag to note the vehicle number and Work Order ticket.
Designate a Warranty Shelf
Parts that are being replaced under warranty should be kept in a separate area. This will help staff know not to use them on other vehicles, and will help managers track what’s being covered versus what needs to be ordered new. Like the special-order items, these parts can also be tagged with a twist tag to note the vehicle number and Work Order ticket.
Label a Core Shelf
Parts rooms should have an area marked and labeled for return core parts. Staff members can make a note on each part to state when it is to be returned, and reference the Credit Purchase Order.
Create Clear, Descriptive Naming Conventions for Parts
Operations should determine a naming convention for all parts so items are labeled consistently. This will help when taking inventory, ordering new parts and looking for items in the parts room.
Use Barcodes
Attaching barcodes to parts bins and parts will help operations easily take inventory of what parts are in-stock. This will help staff members quickly locate parts, check what’s on-hand, and allow for employees to return unneeded parts to their correct designated places.
Take Inventory Regularly
Performing inventory regularly – monthly or quarterly – helps parts rooms better track what’s on-hand. It also helps rooms stay organized as any mislabeled or misplaced parts can be put back in their correct spots. Using barcodes and barcode tools can make the inventory process more efficient.
To learn more about RTA Fleet Management Software’s barcoding tools, contact us today to request a free demo.