Road Tested: RTA’s Fleet Management Software Features
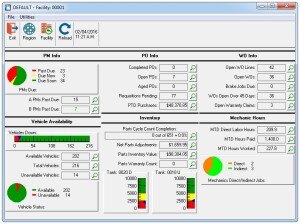
Designed to save your fleet money, keep your management organized and increase efficiency, RTA’s fleet management software features originated from one of the industry’s biggest names.
Ron Turley had one of the first authoritative voices in the fleet industry, and his influence continues today. Before founding RTA in 1979, Ron saved UPS nearly $100 million in vehicle costs during five years as their national director of maintenance. Adjusted for inflation, that figure would be more than $300 million today.
RTA fleet management software takes the best practices Ron developed during his time with UPS and makes them available to fleet managers everywhere.
RTA’s Software Features Make Fleet Management More Manageable
Fleet managers are in charge of a long list of tasks, including preventive maintenance (PM), parts tracking, warranty recovery, training, budgeting, shop management and much more. In turn, fleet management software should keep track of all of this data to make management more efficient.
And RTA’s fleet management software does just that. Put simply, RTA’s fleet management software acts as a company-wide calendar for all facets of scheduling, a point of communication between employees, a tracking system to monitor vehicles and a virtual filing cabinet with easily accessible data information and history.
RTA’s Primary Fleet Management Software Features
RTA’s software is filled with features to help your fleet run smoothly. Although each feature is beneficial, the primary features include:
- Preventive Maintenance Tracking and Scheduling
Preventive maintenance keeps vehicles in operating condition at the lowest possible cost. A highly functional PM program requires an accurate schedule, a well-trained mechanic, a quality control program and an efficient form and system.
RTA’s PM software tracks these items, makes them as efficient as possible, generates records of vehicle inspections, repairs, part failures and more. Ron Turley frequently shared that three to eight hours are saved for every one hour invested in PM, so RTA’s software makes it easier to track the details and save fleet managers a great deal of time.
- Parts Inventory and Warranty Tracking
A key component to a fleet’s success is managing the accurate number of parts and ensuring the right parts are available. In fact, Ron estimated that most fleets stay under-stocked on 35-40% of parts and overstocked on 25%. This software feature enables shop managers to track inventory for all parts, including handheld barcode readers.
Additionally, warranty tracking with RTA’s fleet management system notifies a mechanic when a repair is covered under a variety of warranties, including:
- OEM (e.g. bumper-to-bumper)
- Extended (e.g. powertrain)
- Component/after-market (e.g. parts)
When a repair is flagged as a warranty item, a mechanic can create a claim in the system and track the collection on that claim from the vendor. Consider that five minutes of warranty paperwork typically yields $110. Now, multiply that number by dozens of parts per vehicle and hundreds or thousands of vehicles to see the potential savings gained by the parts inventory and warranty tracking features.
- Scheduling and Communication
Scheduling is a time-consuming but crucial task for the day-to-day function of a fleet. RTA’s management software includes scheduling and communication features for all branches within a fleet. From driver shifts to regular maintenance, the system acts as a calendar for the entire fleet and even sends reminders so nothing is overlooked and no unnecessary tasks are repeated, which saves money.
In fact, these systems’ scheduling features also act as a platform for communication between drivers, shift managers and mechanics. With note-taking functions, a mechanic may begin his or her scheduled shift expediently by looking at the notes from the mechanic or manager from the prior shift. A schedule paired with clear, easy-to-read notes, requests and overviews enables employees working for a fleet to be more efficient and productive.
System Value Analysis: Features to Match the Fleet Manager’s Growing Needs
RTA has continually evolved and added features over the years to improve fleet productivity. In addition to the primary features, RTA includes modules that manage the following:
- Mechanic productivity
- Mechanic accountability
- Preventive scheduling
- Purchasing help
- Budget help
- Warranty help, repeat repairs, failure analysis
- Parts inventory control
- Fuel inventory
- Reports
- Speed
- Pop-up windows
- Paperless capabilities
- Lifetime detailed history
- On-screen help
- Adaptability to fleet type
- Scheduling for non-PM work
- Close lines on repair orders
Data Gathering
With RTA, the options are virtually limitless when it comes to data collecting, whether pertaining to internal departments or company facilities. Aside from vehicle tracking, inventory tracking and vehicle condition data, RTA also monitors:
- Fuel usage
- Oil consumption
- Part failure
- Brake wear
- Routine maintenance
To learn more about finding the right management software for your fleet, click here.