What A Cost-Effective Fleet Looks Like
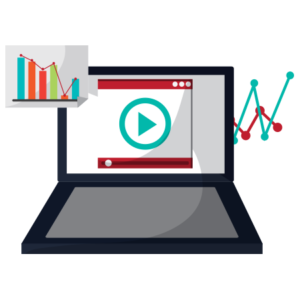
Have you been tasked with streamlining the fleet's operation to get costs in check? With supplier costs continuing to rise, managers are faced with the daunting challenge of cutting expenses. This can be a delicate balancing act. As it may seem easy to simply cut the larger ticket items first, let's take a look at the low-hanging fruit and the organization within the organization.
What are the organization's policies, procedures, and goals? Take the time to review business plans and internal operating policies to ensure these documents are in line with local, state, and federal laws. If you are a governmental-based agency, check against local codes, ordinances, and charters. Check to see that policies are updated and inline with safety in mind. Make sure your organization meets its stated goals, at a minimum, on a monthly basis.
Data and Performance Management
Ensure ample data is collected within your organization and managed by a comprehensive and robust fleet management software. Having a solid foundation in which to collect data is the basis for being able to generate accurate reports. Reporting which provides useful data management requires to make informed and educated decisions. Have the ability to collect data on preventive maintenance schedule, work order history, purchasing history, parts inventories, labor analyses and more.
To eliminate data entry errors, move from manual data entry to a barcoding system. Eliminating manual data entry saves time and money across the board and virtually eliminates error. The RTA solution comes programmed with barcoding included.
Stewardship and Safety
- Train staff on fuel-efficient techniques and implement policies such as an idling policy and fuel-efficient driving techniques
- Manage waste streams coming from the fueling and shop areas in a safe manner
- Train staff on proper handling of waste and hazardous materials
- Provide routine (at least annually) equipment operation training
- Track and review monthly to ensure compliance: licenses and inspections on fueling, equipment, and operator
Customer Service
Observe how staff interacts with not only each other but with clients and vendors. Ensure the communication is consistent and in line with company policies and goals. Keep communication consistent and on-going in order to help smooth out operational processes.
Equipment Specifications
When determining equipment specifications prior to purchase, ensure there are standardized and uniform details across the board. Involve those who operate and maintain the equipment. This not only improves overall operation of the shop, but it improves communication, and increases morale. Those who operate and repair the equipment must be involved. Specifications should also include detailed warranty information. When purchasing fuel obtain multiple bids to ensure the lowest price available. Review fueling reports daily, weekly, monthly and monitor levels when fuel is kept on hand.
Replacement and Disposal Plan
Create guidelines and/or a policy as to when, at a minimum, equipment can be replaced, that equipment has maximized its value, and when to remove equipment from fleet once it has been replaced. Address any parts or supplies that on hand so that inventory levels can be adjusted and unwanted parts are not left on the shelves. Establish a process where money is set aside annually to fund replacement vehicles. This eliminates the need of securing financing.
Knowing life-cycle costs on assets with a system such as RTA Fleet Management Software will help management determine when it's time to replace the asset. RTA offers a robust tracking and asset management system to help fleets become cost-effective and efficient.
(c) 2017 Ron Turley Associates, Inc. | (800) 279-0529 | www.rtafleet.com