Case Study: Arizona Department of Corrections Powers Fleet 100 with RTA
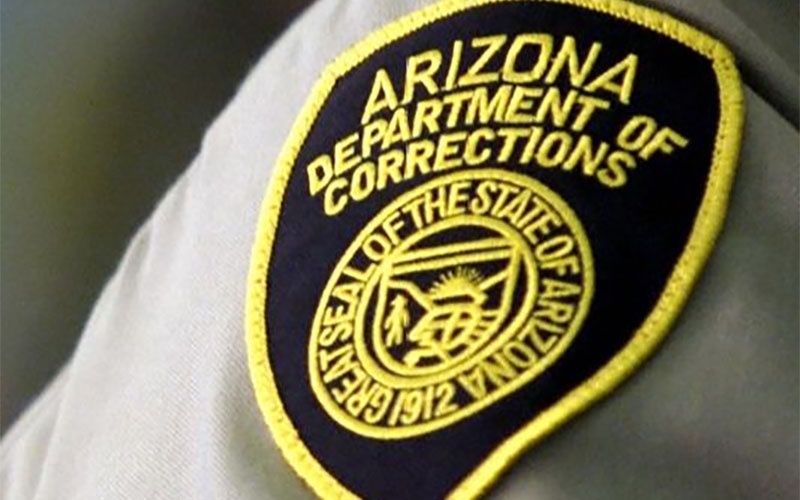
About Arizona Department of Corrections
Headquartered in Phoenix, the Arizona Department of Corrections (ADC) has more than 9,500 staff members to work at its 10 state-wide prisons and oversee more than 40,000 inmates.
The ADC has about 2,455 vehicles and equipment, which are maintained by its fleet management department. Its 13 repair facilities are staffed with 10 Equipment Repair Technicians, three Lead Equipment Repair Technicians and 10 Equipment Shop Supervisors to keep all of the ADC assets up and running.
ADC Was Understaffed to Service its Large Fleet
With close to 2,500 assets to maintain and a small, dedicated team, the ADC’s fleet management department was consistently under-staffed. The department determined its ratio of technicians to equipment was 1:189. This left them about 13 technicians short of what they figured they needed to properly service the assets.
To supplement its staff, the fleet department used inmates to help with routine tasks. However, inmates weren’t experienced in fleet maintenance, and at most could only assist the full-time, certified technicians. The fleet operation also experienced a high turnover of inmates in the shop as they were reassigned to other departments or completed their sentences, making it difficult to train and develop skills in the inmates.
The department was also facing an overall ADC challenge of reducing the number of return inmates. The ADC as a whole set a 10-year goal of trying to achieve a 25-percent reduction of inmates who return to incarceration.
Fleet Management Department Created Fleet 100 Program
To help the fleet management department both decrease the technician-to-asset ratio and help inmates develop skills that will benefit them outside of prison, Jeffery Dickman, the Equipment Shop Supervisor at ASPC-Yuma, created the Fleet 100 program.
To ensure all vehicles at ASPC-Yuma were maintained at a 100-percent level of operational readiness, Dickman started getting inmates more involved with the repair process. Instead of having them assist the technicians, the inmates started getting Work Orders assigned to them through the RTA system. After noticing the inmates didn’t have the experience or skills to help them work in a shop outside of prison, the shops were transformed into training facilities. The inmates worked in various positions that would exist at a real shop, learning skills that would benefit them outside of prison.
By doing this, the technicians became the trainers — there to assist and educate — and the inmates worked as technicians. This increased the size of the maintenance staff at Yuma. The program enabled more work to get done, and provided inmates with hands-on, real-world experience and training that could help them obtain a job and reduce the likelihood of them returning to prison.
Inmates are Learning Skills While Reducing Labor
After the success at Yuma, Fleet 100 was rolled out to the other ADC fleet management departments. The department sought out inmates who had at least 3 years left of their sentence to take part in the training program. This ensured the inmates had enough time to learn skills, and gave the fleet department assurance that they wouldn’t have a revolving door of inmates that they would need to keep training.
To assist inmates in finding work after prison, the Fleet 100 program included using RTA’s Paperless Shop program to record which Work Orders and repairs inmates have completed. Each inmate is set up as an employee, and he or she logs onto a thin client that only has access to Paperless Shop and Paperless Inspection tools. The department runs weekly and monthly productivity reports on each inmate to track their Work Orders.
Inmates can then take these reports and use them as part of a resume when they leave prison and are looking for employment.
After being rolled out in January 2019, Fleet 100 has been an overall success. Richard Kauth, Maintenance Operations Manager at ADC, said he hasn’t had any negative feedback, and the inmates appreciate the opportunity to learn skills and a trade they can benefit from when looking for employment.
“They want to help themselves,” Kauth said.
Fleet 100 has seen multiple benefits in its initial rollout. The fleet management department is saving money by using inmates for additional tasks, and more service requests are being completed. The inmates are benefiting from not only learning new skills, but they are also developing teamwork skills as they work with people of different racial and cultural backgrounds in a work environment.
“We’ve taken it to a different level that wasn’t expected, and the results are showing,” Kauth said.
The next goal of Fleet 100 is to partner with second-chance employers who can offer job placements for inmates after they are released.