6 Ways to Maximize Your Fleet Operation’s Warranty Recovery
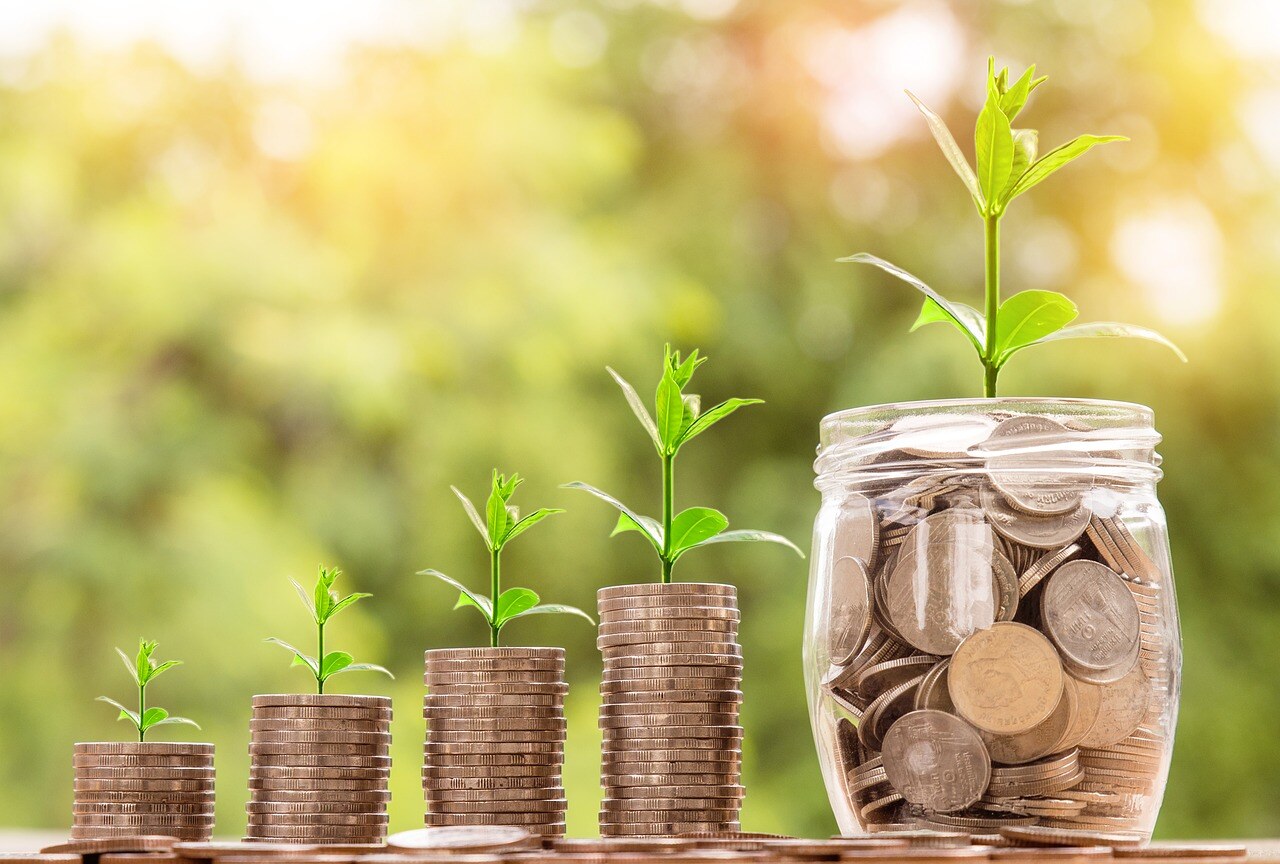
When looking to improve your fleet operation’s bottom line, don’t overlook the importance of warranty claims. Warranty recovery can be one of the quickest ways to add money to your operation.
Operations can leave thousands of dollars on the table in unclaimed warranties each year. Use the following tips to ensure your operation is maximizing its warranty recovery.
Recover Lost Revenue
A common reason for operations to fall behind in their warranty recovery program is due to time constraints. While creating and maintaining a program can take an initial time investment, it can be worth it. As a rule of thumb, 5 minutes of paperwork generally yields $110 of warranty. So, 45 hours of work could result in $60,000 in recovery. If the labor for 45 hours cost the operation $2,800, the investment would pay out 20:1. This return on investment could make warranty recovery one of the most profitable operations in the shop.
Maximize Small Parts Warranties
When claiming warranties, don’t overlook the small parts. While most operations will get warranties on engines, transmissions, rear ends and other high-priced parts, small parts can still generate a lot of money in warranty recovery. It’s estimated tens of thousands of dollars are wasted due to the lack of attention to small parts warranty claims.
To correct this, operations should use fleet management software to track parts and their warranty information. If warranty information is entered for each part, the technician will be able to check in the software system if each part he or she is replacing is under warranty. If it is, the technician should tag the part with the vehicle number, the odometer reading and the date of the replacement. The software solution can then generate a list of all warranty parts replaced, which will provide the necessary information for filing claims.
Keep Failed Components
When replacing failed parts, it’s important to not dispose of them immediately. To redeem the warranty, some manufacturers require inspection of the part or component before approving the claim. A general rule is to keep all failed parts in a designated place (a box or bin) for 45 to 60 days before disposing of them.
Understand Parts, Component Failures
Even when parts are covered under warranty, it still results in downtime for vehicles to replace the failed components. To minimize the repair time – and to prevent recurring issues – the operation needs to find the cause of the failure and how it could have been caught earlier. The best way to do this is to perform systematic analysis of all failed parts.
Performing failure analysis will help identify more than just errors with the part. It will also provide insight on areas where the operation can improve. Some areas can include:
- Preventative Maintenance: Determining the cause of failure can determine if an operation’s PM intervals are set correctly. If the failure was due to waiting too long between PM appointments, thus not allowing the failure to be detected earlier, then schedules might need to be adjusted.
- Vehicle Inspections: The failure analysis could show that a type of part was not strong enough for that particular vehicle. That can alert the operation that larger or different parts will need to be ordered in the future.
- Driver Training: If the failure analysis shows driver error contributed to the part failure, then more driver training can be needed to prevent more issues in the future.
- Mechanic Training: A failure analysis can also reveal technician errors – either mistakes in the way repairs were made, or lack or attention to certain parts. Additional training can prevent these.
Invest Time Now to Save More Time Later
When vehicles go into shops for repairs, it can be tempting for operations to fix the issue and get the vehicle back on the road as soon as possible. Technicians can quickly change out parts and minimize downtime. However, doing it this way doesn’t allow time to figure out why the part failed.
Determining the root cause of a part failure can take longer initially, but this can help the operation both determine if the part was under warranty, and if the failure is due to a larger issue. This allows the problem to be detected and fixed and can prevent the vehicle from returning to the shop sooner.
Don’t Neglect the Driving Environment
When performing a failure analysis, the result can show that the problem isn’t with the part itself, but rather with the driver or the operating environment. Driver abuse, overloads and rough operating conditions are only a few of the outside influences that can cause component failure sooner than expected.
The following tips can help prolong components lifespans, and help recoup warranty claims:
- Analyze Repair History: Service records can help the operation determine if an issue was a chronic problem with the vehicle or an isolated issue.
- Handle Failed Parts Carefully: Even when a part fails, it still needs to be handled carefully when being removed from the vehicle and stored. If a part rusts or deteriorates, it can be more difficult to inspect or evaluate when diagnosing the problem and submitting the part to the manufacturer for a warranty claim.
- Don’t Overload Vehicles: Overloading a vehicle can cause body breaks and can be the most costly of all tire abuses.
- Keep Tires Properly Inflated: Not keeping tires at the correct pressure can result in more wear and tear, and potentially lead to more blowouts.
RTA Fleet Management Software is committed to helping your fleet operation maximize its warranty recoveries. Contact us today to find out how RTA can help your operation get more money back on claims.