4 Ways to Leverage Fleet Data to Improve Your Operation
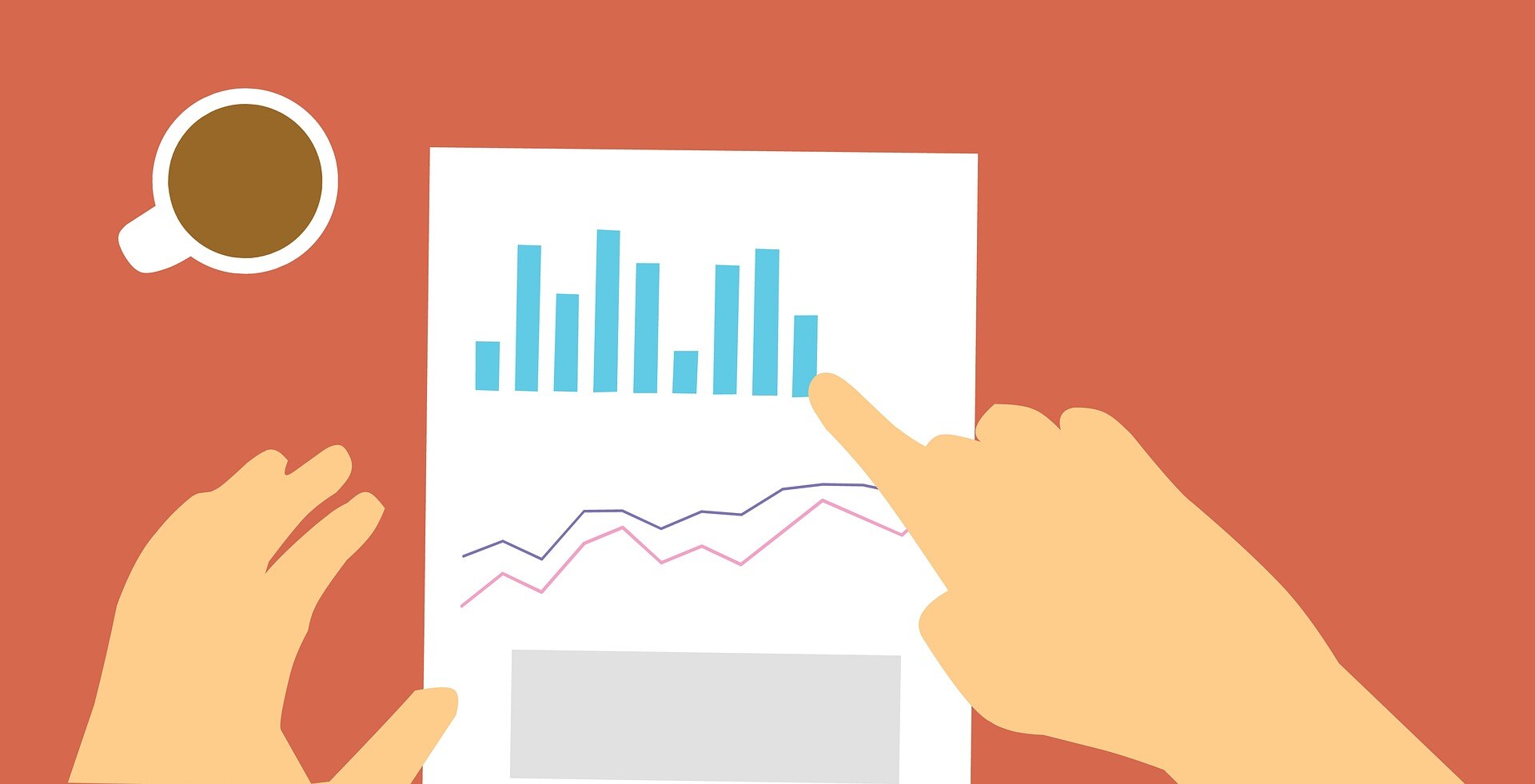
There is no shortage of data in fleet operations. In fact, most operations are swimming in the vast amounts of information collected each day. The challenge is to use the data to the benefit of the fleet, which is a struggle for organizations across all industries.
According to McKinsey, “86 percent of executives say their organizations have been at best somewhat effective at meeting the primary objective of their data and analytics programs, including more than one-quarter who say they’ve been ineffective.1”
If used correctly, data can improve a fleet operation and increase its efficiency. To get to that point, the right data needs to be collected and then utilized in a way that it can improve a fleet operation’s workflow and bottom-line.
TRACK THE RIGHT DATA
With so much data being collected each day, it’s important for fleet operations to pinpoint which information is most important to their operation. Quick and accurate data is a fleet manager’s greatest tool in reducing waste, eliminating redundancies and preventing problems before they occur.2 Fleet managers need to identify the analytics that will help them do their jobs better and more efficiently.
Some of these might include:
Fuel Usage and Costs: Fuel is typically a fleet’s largest expenditure, and fuel economy can be impacted by nearly everything. A fuel-tracking system provides data on fuel totals and spending for each vehicle.
Tire Performance and Costs: Tires can have a big impact on overall fleet costs. Tire-tracking systems monitor the performance of each tire and the cost per mile.
Vehicles and Equipment Usage and Costs: Repair history, cost per mile, license and insurance information, and vehicle replacement are all critical information to store on vehicles and equipment. Operations need data on overall costs and incremental expenses (per mile, per year, etc.) to properly determine which equipment and vehicles are running efficiently.
Parts Inventory, Usage and Costs: Tracking parts inventory allows parts room managers to stock more efficiently, allowing for better turnover ratio and elimination of obsolete or slow-moving parts. Operations need to know at all times how many parts are available, how many are being used, the average life span of each part (by model and vendor), and overall costs.
Driver Data: Individual driver information can be an important tool in identifying areas that need improvement or analyzing which drivers need further training. Telematics and GPS data can inform operations of negative behaviors like speeding, sudden braking and accelerating, and distracted driving. Data can also be used to track driver accidents and citations. Electronic Logging Devices (ELD) can also track information on driver statuses.
Labor Hours and Costs: When time is money, fleet managers can’t afford wasted technician hours. Shop management tools provide data on how time is actually spent on value-add activities and which technicians may require additional training, allowing you to boost the productivity and cost-effectiveness of your shop.
Total Cost of Ownership (TCO): TCO information on individual vehicle makes and models ensures poorly performing vehicles aren’t consuming capital.
ANALYZE DATA TO MONITOR PERFORMANCE
While collecting data is important for fleets, it will not benefit an operation unless it is analyzed properly. Fleets must know how to interpret and use the information being delivered to make improvements to their operation.
To properly analyze data, fleets need to know what information is important to their operation:
Once a fleet manager can answer those questions, he or she can start to analyze the data in the following ways:
Set Key Performance Indicators (KPIs): There is no right or wrong list of KPIs to measure – it just depends what information is important to an operation. A good way to start is by looking at the list under Track the Right Data. Fleet managers can determine which of those areas are most crucial to their fleet operation’s performance, whether it’s measuring parts usage, tire costs, labor costs or productivity. Once determined, the data from those categories should be analyzed to determine how the fleet is performing.
Create Dashboards: To track KPIs, fleet managers should set up dashboards so they can easily access the data that’s most important to their operation. This allows fleet managers to quickly see information and react, if needed.
Determine Benchmarks: When monitoring the KPIs, fleets should determine benchmarks for where the data should span. These can be determined by looking at information from past years or months to see how the operation typically performs in each category. Then, over a designated time period, the data can be pulled and analyzed to see how the fleet is currently performing. Fleets can also look at industry averages when looking at the numbers and set benchmarks against those trends.
Set Goals and Objectives: When analyzing data, fleet managers should consider the operation’s overall goals and objectives. Measuring against these will help managers determine how the fleet is tracking long-term and if it is working towards accomplishing those objectives.
USE DATA TO SAVE MONEY
Using data in the right way can save fleet operations money. Tracking information about a fleet can reveal areas of inefficiencies and potential cost savings.
Track Parts Inventory Usage: Fleets need to balance how many parts they are using versus how many they are keeping in inventory. Monitoring data related to which parts are being used and how many are left in stock will help fleets save money on re-stocking unnecessary parts. It will also save in vehicle downtime by ensuring there are parts on-hand to prevent long maintenance windows.
Watch Tire Usage: Replacing tires can be costly for fleets. Monitoring data related to tire pressure, rotations, balancing and scheduled maintenance can help operations prolong the life of the tires.3 Keeping the tires properly maintained can also help fleets manage fuel costs.
Monitor Fuel Costs: As one of a fleet’s largest expenses, it’s crucial to track fuel costs across an operation. Fleets can monitor the miles per gallon vehicles are using, and cross-reference that information with the miles per gallon the vehicle is capable of to see if the vehicle is reaching its potential.2 Tracking fuel costs will also help fleets determine if drivers are using fuel for personal use.
Measure Labor Costs and Inefficiencies: Data can provide insight into labor hours and productivity. Fleets can monitor how many hours technicians are logging and see how long they are spending on each individual task. Tracking how long jobs take can help fleets identify where there are inefficiencies in the workflow. For example, if technicians are wasting time looking for information about a vehicle or the availability of a part, then giving technicians access to the data in the fleet management system will allow them to obtain the needed information in real-time. Identifying issues like these and correcting them will help make the fleet more productive and save money on wasted labor.
USE DATA TO HELP LEVERAGE REQUESTS OF SENIOR MANAGEMENT
Data is hard to argue with, especially when presented to upper-level management. Knowing the ins and outs of a fleet operation with numbers to back it up is a good way to leverage requests with management teams.
In McKinsey’s survey, the biggest reason companies were able to be effective using data and analytics was due to the involvement of senior-level management. Twenty-five percent of surveyed businesses stated their superior’s participation helped data usage be more effective.
Setting up data to show the fleet’s performance against key company and departmental objectives will show senior management the impact of the fleet operation. Presenting data from intervals throughout the year – monthly or quarterly – will demonstrate how the fleet is trending year-to-date, and where it is forecasted to finish at year-end.
Showing trends in the data and giving detailed analysis will help upper management feel connected with the fleet’s performance and needs, as well as trends in the industry. This can make future requests easier when the data is already showing where the improvements and investments need to occur.
CONCLUSION
In conclusion, using data in the right way can help fleets improve their operation. Fleets need to identify the types of data that will help impact their operation the most. To do this, organizations need to establish goals and objectives they can track towards. Monitoring these key data points and watching the information closely will help fleets save money, and will give operations concrete information they can elevate to their superiors to get requested technology or resources.
RESOURCES
1 “The Need to Lead in Data and Analytics,” McKinsey, 2016. https://www.mckinsey.com/business-functions/digital-mckinsey/our-insights/the-need-to-lead-in-data-and-analytics
2 Best Practices for Fleet Managers https://www.rtafleet.com/fleet-university/learning-materials/white-papers/
3 Controlling Tire Expenses https://www.rtafleet.com/fleet-university/learning-materials/white-papers/
4 Fuel Econony, https://www.fueleconomy.gov/feg/maintain.jsp
Learn how RTA’s FMIS can help you access the data you need to make data-driven decisions and improve your fleet’s performance.