4 Ways To Make Your Trucking Operation More Efficient
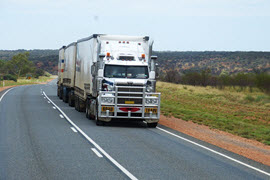
When Jeff Jenkins took over as CEO of a mid-sized trucking operation, he was tasked with getting this operation out of the red after it was losing millions of dollars each year.
For Jeff to right the ship and stop the company from hemorrhaging money, he needed to make the operation more efficient with its resources.
At RTA, we consider Resource Efficiency one of the Four Pillars of Fleet Success (along with Stakeholder Satisfaction, Intentional Culture, and Risk Management). We define this as: “Making the best use of your two most finite resources – time and money.”
Learn how Jeff made his fleet more efficient by saving time and money and get tips that you can use at your operation.
- Evaluate Your Personnel
Your employees are your most valuable resource at your fleet operation. If they are not using their time wisely, being as productive as possible, and fulfilling the right roles, then your operation cannot be efficient.
When Jeff took over as CEO, he got a lot of complaints from staff members saying they were overworked. In the past, the company just hired more employees. However, this led them to be overstaffed by about 10 people. Jeff decided to take a different approach. He met with each employee to see if there were redundancies or inefficiencies they could eliminate to make the staff more productive.
One of the most important tasks he did was to evaluate how the technicians were using their time. The company was not tracking technicians’ time per job and there were no standards in place for how long each job should take. Jeff worked with his staff to determine a standard set of repair times for various jobs. Now they could measure how productive each tech was, and could easily identify if there were training needs on the staff.
If your trucking operation doesn’t have a set of repair times to measure technicians by, you can do what Jeff did and create your own. You can also use published Standard Repair Times in guides like Mitchell OnDemand, Motor, or Chiltons.
- Organize Your Parts Room & Purchasing
How organized is your fleet operation’s parts room?
Without an organized parts room, your operation can be wasting money keeping old parts on shelves (that might not even work in the vehicles currently in your fleet), or buying unnecessary parts because you can’t find them in your shop. Organizing your parts room allows you to see how many of each part you have in stock, lets you eliminate outdated parts, and saves your parts room staff and technicians time when locating the parts they need.
In addition to keeping the room organized, it’s also important to evaluate how much you are paying your parts vendors.
When Jeff joined the trucking company, one of the first areas he started making changes to was the parts room and parts costs. He discovered that the operation was buying premium, top-of-the-line tires at retail prices (about $900 for one steer tire). After the company didn’t want to renegotiate, Jeff opened the bidding process to new vendors and found more generic tires for about $350. Sure, the quality was less, but at a $550 savings per tire, he could afford to replace the tire almost three times for what one tire was currently costing them.
Renegotiating the tires contract and other parts contracts resulted in a savings of about $1 million a year.
- Monitor Your Fuel
Fuel is one of your trucking operation’s largest expenses. Because of this, wasting any fuel at all can add up quickly. To prevent this, it’s essential to evaluate how your fuel is being used.
This can include monitoring your drivers’ behaviors to see if they are spending too much time idling, for example, or if they are going off-route and wasting fuel.
It’s also important to track which trucks are using the most fuel. This can identify if an asset is getting too costly to operate and needs to be replaced.
At his trucking operation, Jeff had to enforce rules about when drivers could bring trucks home versus when they needed to stay at the operation. The rule was supposed to be if you lived within 10 miles of the operation you could drive the truck home. However, not all drivers were following this mandate and were driving much farther to their homes each day. It resulted in hundreds of miles of wasted fuel. To curb this, Jeff reinforced the rule and put new parameters in place.
- Utilize Technology
Using new technology can help your operation save both money and time.
As mentioned in the above section on Fuel, operations can use telematics tools to monitor drivers’ behaviors to check for excessive idling, aggressive driving, and track their routes. Telematics can help you identify issues with your vehicles. The system can alert you to a problem so the shop can determine if you need to return for immediate repairs.
Using fleet management software can also help your trucking operation become more efficient. An FMIS can help you eliminate paper forms to save time doing manual data entry and prevent wasted time trying to locate information. An FMIS allows you to store information all in one place.
An FMIS also allows you to run reports and collect data in real-time. This helps you better manage your fleet and keeps you aware of any trends or information you need to know.
Other technology you can implement at your fleet includes fuel management systems. Fuel management systems can instantly track fuel usage to determine which vehicles are using too much fuel and if fuel is being misused. These solutions can also eliminate the need to manually record fuel information – letting you avoid the risk for manual errors.
There are many more methods you can use at your fleet operation to save time and money. The key is to evaluate the processes you are currently using and identify where you can be more efficient.
To learn more about Resource Efficiency and how you can save your fleet operation time and money, join us at the Fleet Success Summit, April 20-21, in Phoenix.