What’s the Real Cost of Vehicle Downtime for Your Fleet?
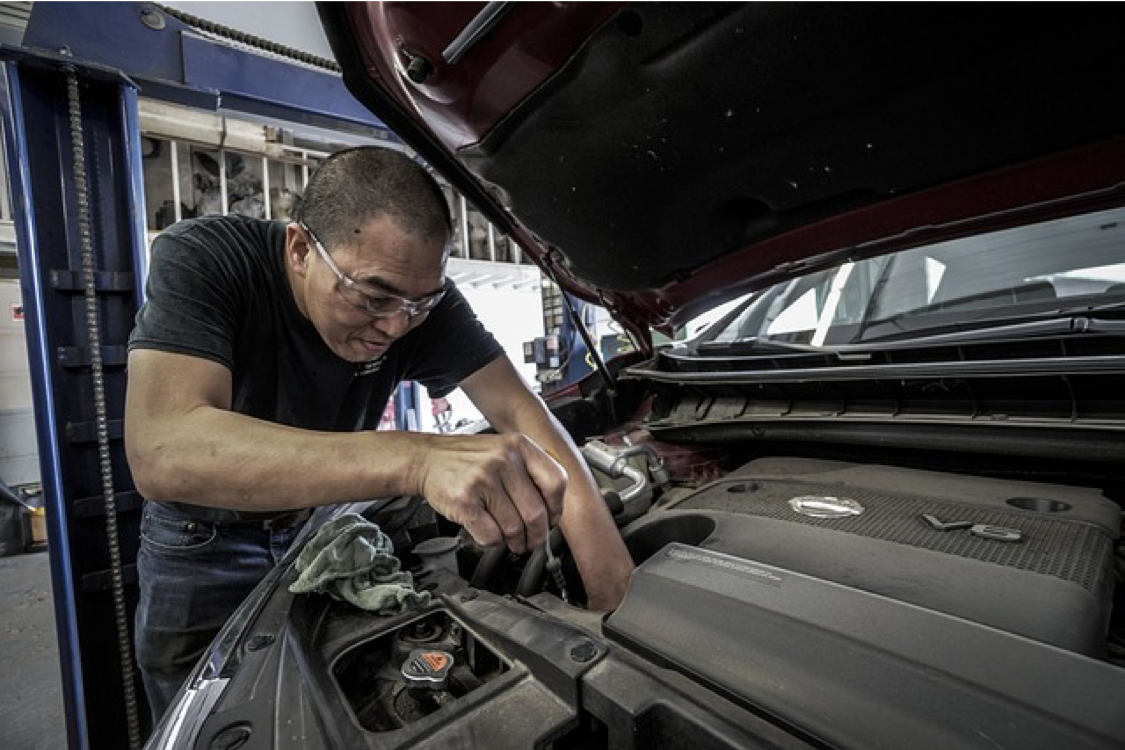
When a vehicle breaks down unexpectedly, it can result in numerous unplanned costs for your fleet operation. These costs – both hard and soft – can cause a major blow to your operation’s budget.
The extent of the expenses can vary depending on how long a vehicle is out-of-service. According to Automotive-Fleet.com, downtime costs should be calculated from the time the vehicle becomes out of service until the driver is able to use it again to resume work.
Take a closer look at some of the costs associated with vehicle downtime.
Hard Costs
When a vehicle breaks down, there are several hard costs associated with it that will directly impact your budget. Some of these can include:
- Labor: When a vehicle needs immediate and unplanned repairs, it can require additional labor hours to quickly fix it. This can result in more technicians working on the vehicle, potentially requiring overtime hours.
- Lost Revenue: When a vehicle is sidelined it is unable to perform work, whether that means transporting goods or passengers, or making deliveries. This results in lost revenue for the operation.
- Towing Expenses: If your vehicle breaks down on the road, you might have to pay for towing expenses to get it back to the shop. This is a direct cost that will go against your budget.
- Repair Costs: To get the vehicle back on the road, the operation needs to use labor to repair the vehicle, as well as purchase parts. If the vehicle needs to be sent off-site for repairs, then the total can be even higher.
Soft Costs
In addition to hard costs, there are also additional soft costs that fleet operations can endure when a vehicle breaks down. Some of these costs can include:
- Lost Productivity: When a vehicle is off the road, so is the driver. This can result in lost productivity as that driver is unable to cover routes. Instead, that vehicles’ workload is likely dispersed to other drivers, creating additional work for the rest of the staff.
- Delays in Providing Services to Clients: When a vehicle is off the road, it can cause a delay in services to clients. This can go beyond the initial delivery the vehicle was supposed to make and create negative feelings in the future if the customer feels like they received bad or delayed service.
How to Calculate the Costs
There are various ways for fleet operations to determine the total cost of vehicle downtime. One way to account for the expenses, according to Automotive-Fleet.com, is to total the following:
- Costs of repairs
- Labor costs
- Cost of replacement parts
- Diagnostic fees
- Towing costs
- Driver wages
While this might not account for all of the costs – especially some of the soft costs – it can give your operation an estimate of how much money an unexpected breakdown can cost the fleet.
To learn how RTA Fleet Management Software can help your fleet operation avoid vehicle downtime, contact us today to schedule a demo.