Standardize An Effective Lockout/Tagout Program - Part 2
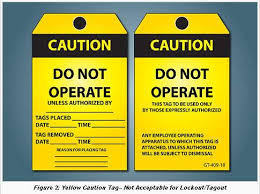
Suggested steps to establishment of an effective lockout/tagout program
This procedure, developed by OSHA, establishes the minimum requirements for the lockout of energy isolating devices whenever maintenance or servicing is done on machines or equipment.
Ensure the machine or equipment is stopped, isolated from all potentially hazardous energy sources and locked out before employees perform any servicing or maintenance where the unexpected energization or start-up of the machine or equipment or release of stored energy could cause injury.
Notify all affected employees that servicing or maintenance is required on a machine or equipment and that the machine or equipment must be shut down and locked out to perform the servicing or maintenance.
Compliance Requirements
All employees are required to comply with the restrictions and limitations imposed upon them during the use of lockout. All employees, upon observing a machine or piece of equipment which is locked out to perform servicing or maintenance shall not attempt to start or operate the machine or equipment.
Note the names and job titles of all affected staff and how to notify each of them.
Staff needs to understand your company's to identify the type and magnitude of the energy that the machine or equipment utilizes, the hazards of the energy, and the types of energy and methods to control the energy.
Process to Lockout Equipment
- If the machine or equipment is operating, shut it down by the equipment's normal stopping procedure.
- De-activate the energy isolating device(s) so the equipment is isolated from the energy source(s).
- Lockout the energy isolating device(s) with assigned, individual lock(s).
- Stored or residual energy must be dissipated or restrained by methods such as grounding, repositioning, blocking, bleeding down, etc.
- Ensure that the equipment is disconnected from the energy source(s) by first checking that no personnel are exposed. Verify the isolation of the equipment by operating the normal operating control(s) or by testing to make certain the equipment will not operate.
- Return operating control(s) to neutral or "off" position after verifying the isolation of the equipment.
Return Equipment to Service
- Check the machine or equipment and the immediate area around the machine to ensure that nonessential items have been removed and the machine or equipment components are operationally intact.
- Check the work area to ensure all employees have been safely positioned or removed from the area.
- Verify that the equipment's controls are in neutral.
- Remove the lockout devices and re-energize the machine or equipment. Note: The removal of some forms of blocking may require re-energization of the machine before safe removal.
- Notify affected employees the servicing or maintenance is completed and the machine or equipment is ready for use.
Establishing a safety program which includes training for all affected employees within a lockout/tagout program will go a long way to ensuring safety and regulatory compliance for your operation. Learn more about OSHA's requirements for safe labor practices by clicking here.
Learn how the various safety components built into the RTA fleet management software solution can help your company remain safe and compliant.