4 Tools to Help Large Fleets Stay Organized
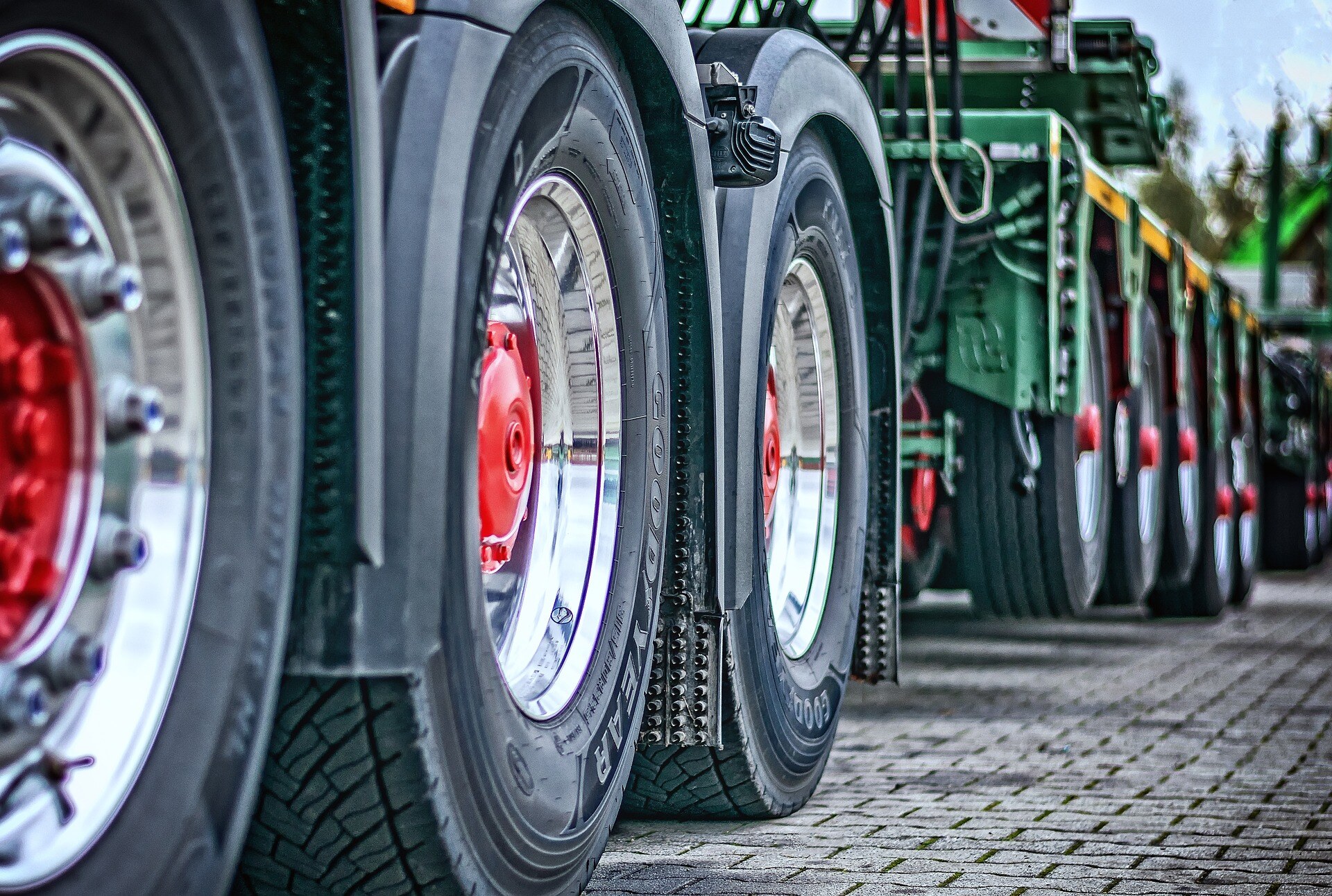
Managers of large fleets face unique challenges to keep their operations organized. Managers must contend with maintaining numerous assets, overseeing large staffs, keeping up with day-to-day tasks, and trying to find efficiencies where they can.
Because of this, fleet managers need tools to help them stay organized. See how using software, custom reports, paperless work orders and barcoding tools can help managers organize large fleets.
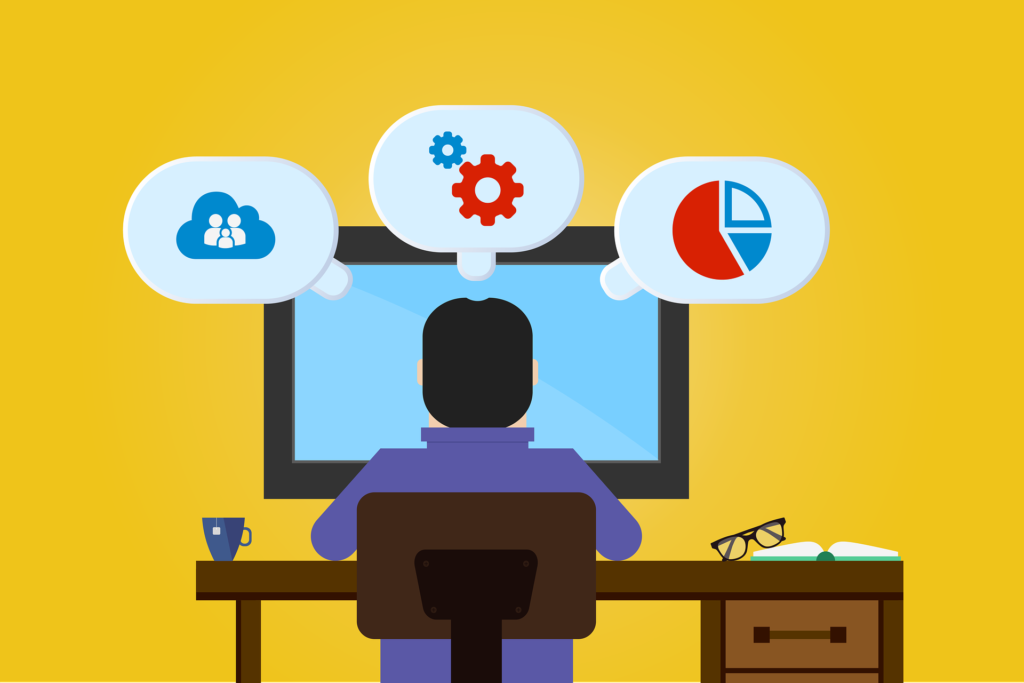
Fleet Management Software
Operations can use fleet management software to keep their information and key data in one location that’s easy to access. Fleet management software allows fleets to store vehicle history, warranties and other information within the system. It also lets operations quickly track preventative maintenance on large fleets through scheduling and work order tools.
Fleet management software allows parts information to be stored in a central location to allow multiple users – and multiple facilities – to access the information. This is key for large fleets with several locations.
Software also enables managers to track key performance indicators (KPIs) and data to monitor the operation’s performance. This allows managers and supervisors to track service requests, work orders, labor hours and other information.
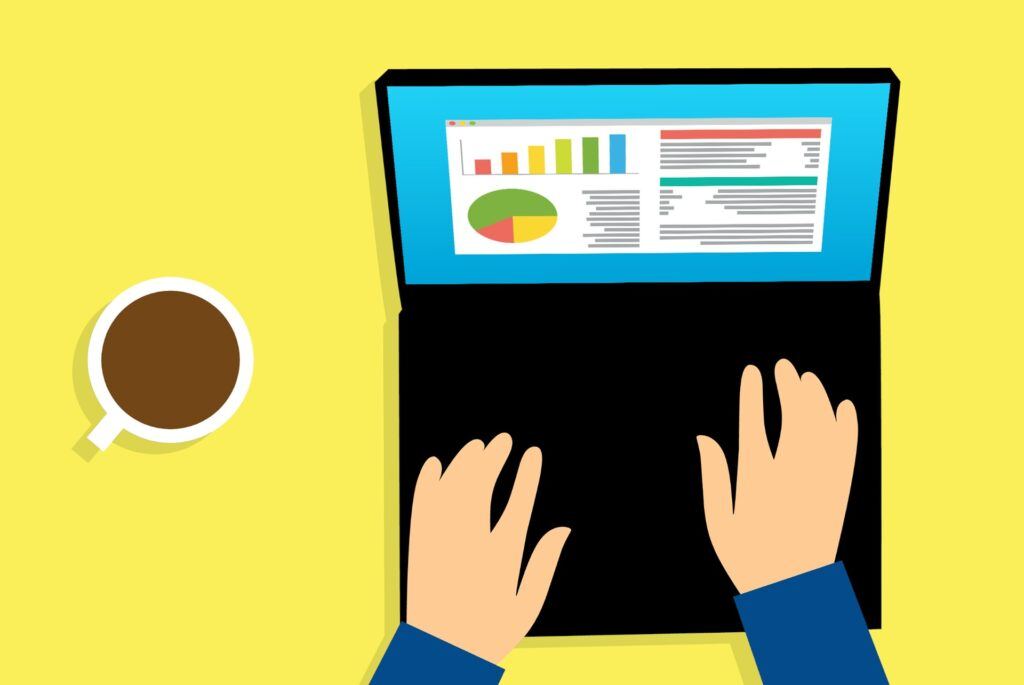
Custom Reports
For fleet managers to track KPIs and monitor the status of their fleet operation, they need to have access to specific data. Creating custom reports within their fleet management software allows managers to pull only the specific data they need and not have to sort through extra information.
Custom reports are also helpful for large fleets because they allow data to be generated by region, facility, etc. Managers can track the entire operation, or focus on a specific area, vehicle or group. This can help measure overall and specific KPIs.
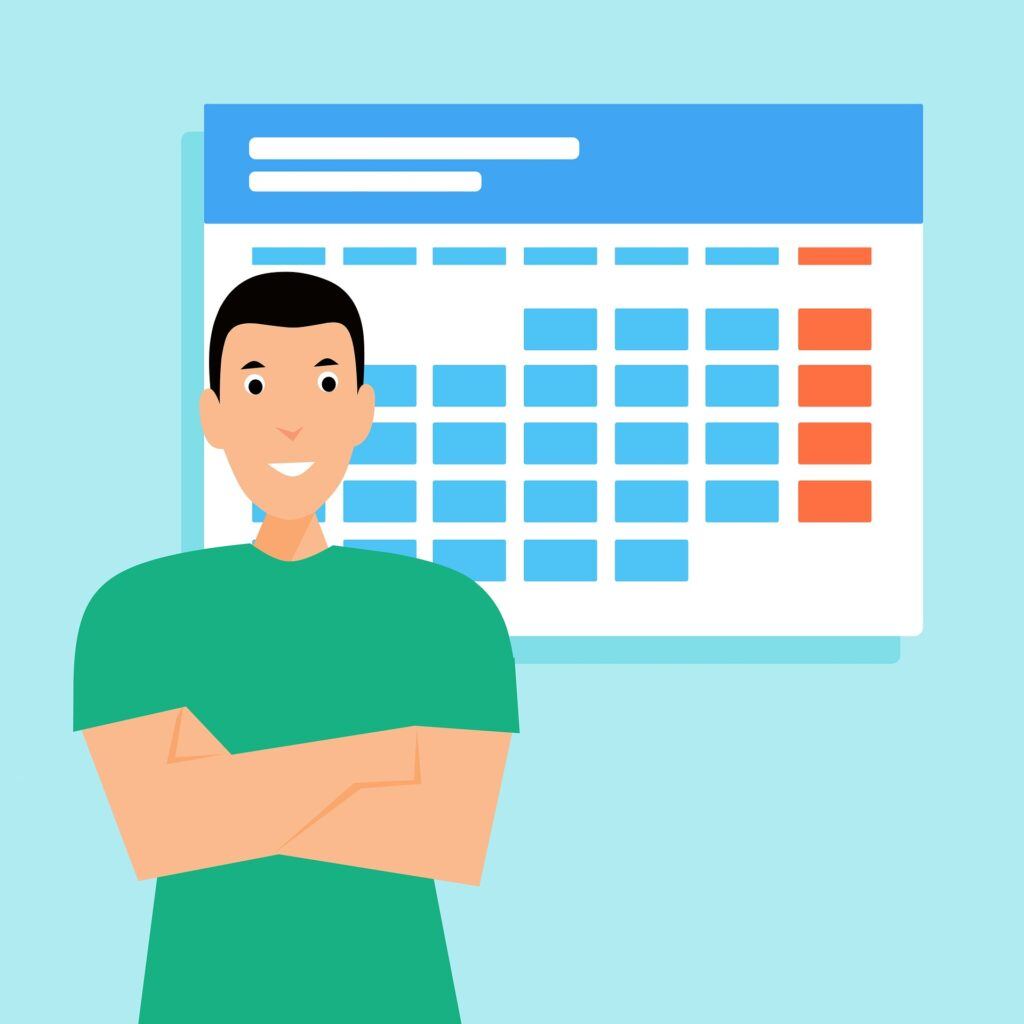
Paperless Work Orders
Work orders can quickly pile up for large fleet operations. This creates a risk of WOs getting lost, misplaced or overlooked.
For fleets who use fleet management software, work orders can be completed within the software system. This allows paperless WOs to be filed for specific vehicles, and lets technicians, shop managers, fleet managers and others access the digital work order at any time. Having these kept in the software system allows fleet managers to pull reports on open work orders, track vehicle maintenance history and warranties, and better schedule vehicles for preventative maintenance.
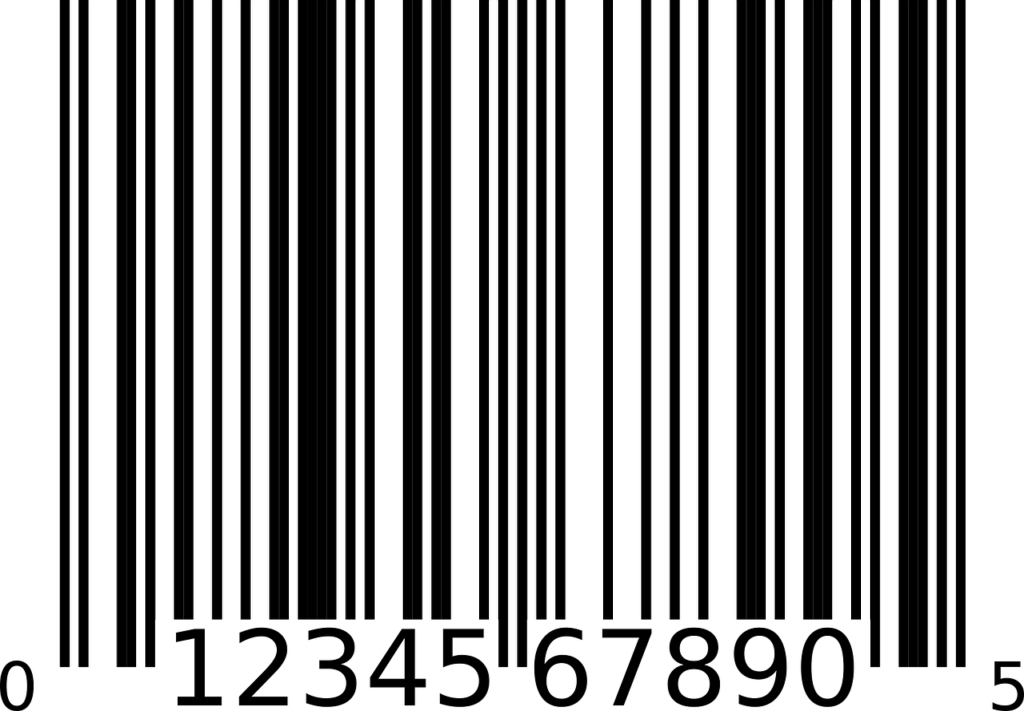
Barcoding Tools
To maintain and service a large fleet, operations need to maintain a vast inventory of parts. Trying to organize and account for so many parts can be a long and tedious task. Barcoding tools can make this inventory process easier. These tools can be integrated into an operation’s fleet management software and allow staff members to create barcodes to label and track parts and their assigned bins. These parts can then quickly be counted into inventory with the use of a barcode scanner.
Using barcode scanners improves the speed and accuracy of inventory. It allows operations to quickly identify mistakes in the inventory, and to change quantities. For large operations, this can save labor. It also ensures there are updated and accurate inventory numbers for all facilities and staff members to access in real-time.
To learn how these tools can help make your operation more organized, contact RTA Fleet Management Software today to request a free demo.