In-House vs. Outsourced Fleet Maintenance: What Fleet Managers Need to Know
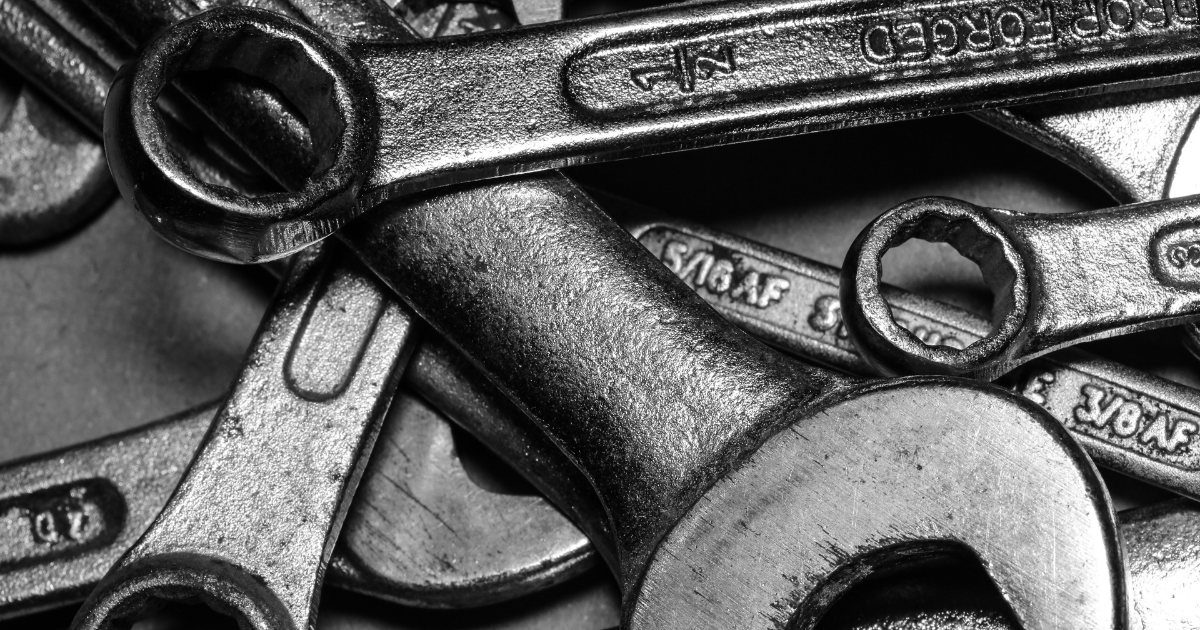
This article is based on a recent episode of The Fleet Success Show podcast. Watch the full episode here:
Introduction: Navigating the Maintenance Minefield
Whether you’re running a municipal fleet or managing hundreds of commercial assets, one question always comes to mind: Should we outsource more of our maintenance, or keep it in-house? With technician shortages and supply chain problems continuing to wreak havoc in the world of fleet, this decision has never been more important—or more complex.
In this Q&A, we tackle fleet managers' most pressing maintenance strategy questions with answers grounded in decades of real-world fleet experience. From managing vendors to minimizing downtime, here’s what you need to know to protect your fleet, budget, and sanity.
Q: Is outsourcing my fleet maintenance worth it?
A: Outsourcing can be beneficial when used strategically, especially for specialty work or overflow. But outsourcing your entire maintenance program without strong vendor oversight can lead to unnecessary costs, reduced vehicle availability, and poor quality control.
Q: What should I include in my vendor contracts?
A: Always include:
- Service level agreements (SLAs) with specific key performance indicators (KPIs) like turnaround time, comeback rate, and communication response time
- Expectations around technician certifications and QA/QC processes
- Penalties for non-performance and rewards for exceeding expectations
Q: What is a comeback rate and why does it matter?
A: A comeback rate tracks how often a vehicle returns for the same issue. High comeback rates signal poor repairs and wasted labor. Vendors should be held accountable for this via KPIs in your contract. If they’re not, you’re eating the cost.
Q: What are the advantages of in-house fleet maintenance?
A: In-house shops give you:
- Direct control over prioritization and scheduling
- Better quality assurance and training
- Cost transparency
- Faster turnaround and reduced vehicle downtime
- Improved tracking with your fleet maintenance management system
Q: How do I avoid being upsold on services I don’t need?
A: Use software for fleet maintenance to track PM intervals, repair history, and parts usage, and compare vendor recommendations against your actual data. If your records show a new starter was installed last month, question the quote for another one. Don’t rely on memory; let your software do the work.
Q: Can I still standardize my fleet if supply chain issues force me to buy different models?
A: You can try, but many fleets have been forced into brand diversity due to vehicle shortages. If that’s your reality, ensure your shop is cross-trained and your software tracks model-specific maintenance protocols. Use software to centralize data, regardless of vehicle make.
Conclusion: It’s Not About Either/Or—It’s About Control
When approached strategically, outsourcing doesn’t have to mean giving up control. But relying too heavily on vendors without oversight is a recipe for missed SLAs, inflated costs, and downtime you can’t afford.
Fleet managers should strive for a hybrid approach (i.e., maintain core repairs in-house where possible, and outsource specialty work to trusted partners). Just remember: The key to any successful strategy is measurement—and your fleet maintenance software is the best tool for the job.
Interested in getting expert advice on how to bring your fleet maintenance in-house? Schedule a conversation today.