5 Steps for Handling Vehicle Recalls
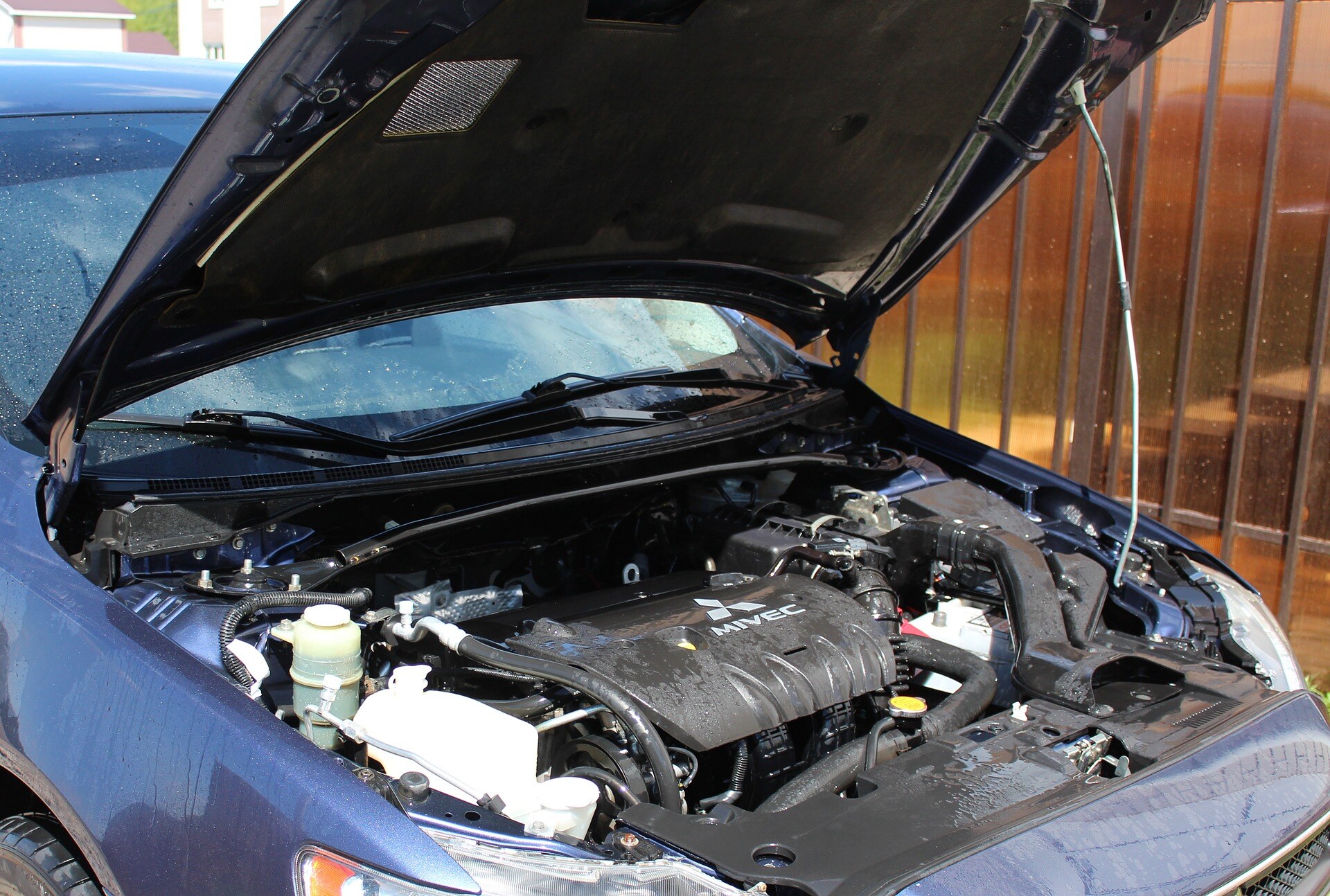
In 2016, there were 927 vehicle recalls issued, which affected more than 53.1 million vehicles, according to the National Highway Traffic Safety Administration (NHTSA). The number of recalls has been rising, according to NHTSA data, which can be troubling for fleets.
With numerous vehicles of varying makes and models, managing and addressing vehicle recalls can be difficult for fleets. To help fleet managers stay on top of recalls, follow these tips on how to minimize downtime while still following safety measures.
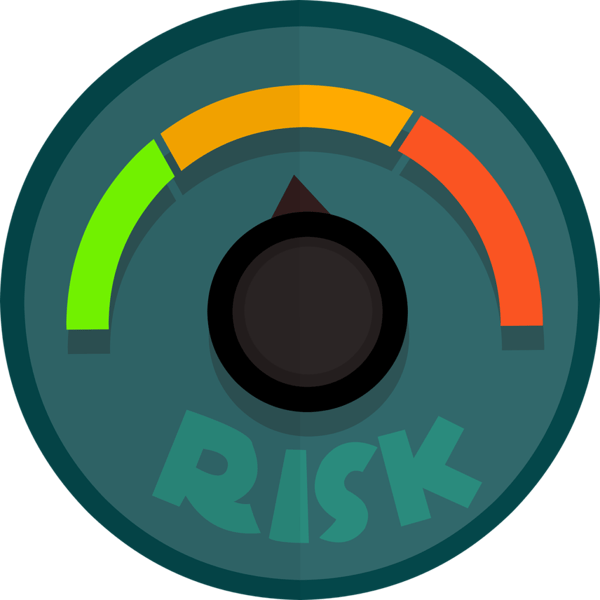
Assess the Risk
Fleets have the responsibility to address all recall notices. While some car owners might think taking care of minor recalls on their personal vehicle is unnecessary, fleets can’t take the risk of ignoring any notices – even if it might seem like an insignificant problem.
Even though repairing recall issues can result in downtime for vehicles, it’s still a must for fleet operations.
“Any unrepaired safety recall could lead to an accident with devastating results to the driver and the vehicle,” Ross Macdonald, chief marketing officer at AutoAp, Inc., told Government-Fleet.com.
When recalls are issued, fleet operations should have a process to determine the level of risk associated with the problem. This can help fleets determine how soon the repairs should be made.
Scott Edwards, CAFM, State of Colorado fleet manager, told Government-Fleet.com the state of Colorado relies on the OEMs to determine the threat level of a recall.
“The OEM has the resources to provide a threat level,” Edwards told Government-Fleet.com. “It is understood that some level of action must be taken on all recalls, or they would not be issued if they were not needed. The information OEMs provide on how a recall should be addressed guides the urgency.”
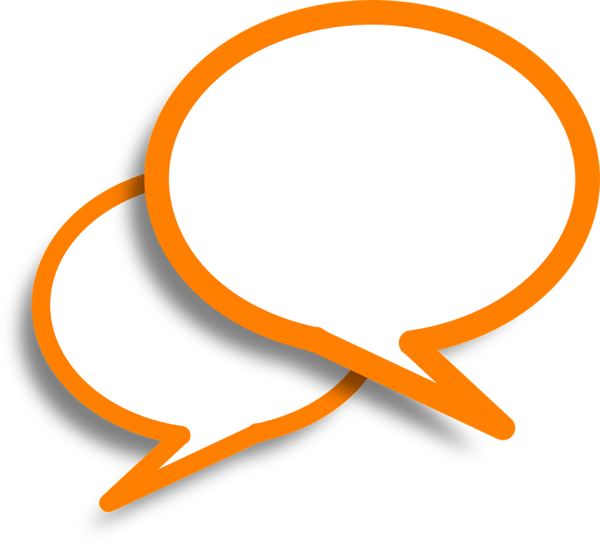
Communicate Recall Information
Once a recall is assessed, those impacted by the recall should be informed, including the drivers and technicians. Recalls can be logged into an operation’s fleet management system to start the repair process, including scheduling repairs, calling certified repair locations if needed, and noting if the vehicle will be down for an extended time.
Drivers should be notified if a vehicle is expected to experience downtime. Drivers should also be informed of what the recall is – no matter the urgency. This will help make drivers aware of what issues to look for when operating the vehicle.
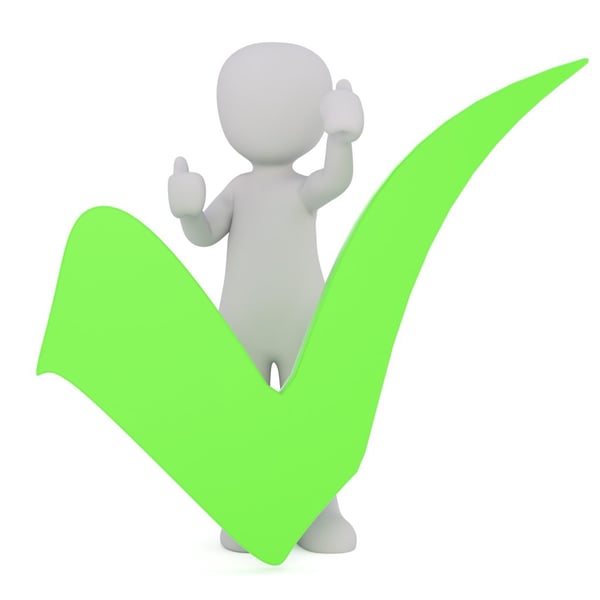
Monitor Vehicle Status
Fleets should monitor the status of vehicles while they are undergoing recall repairs. This will help fleets determine how long vehicles will be down and when they are safe to be driven again.
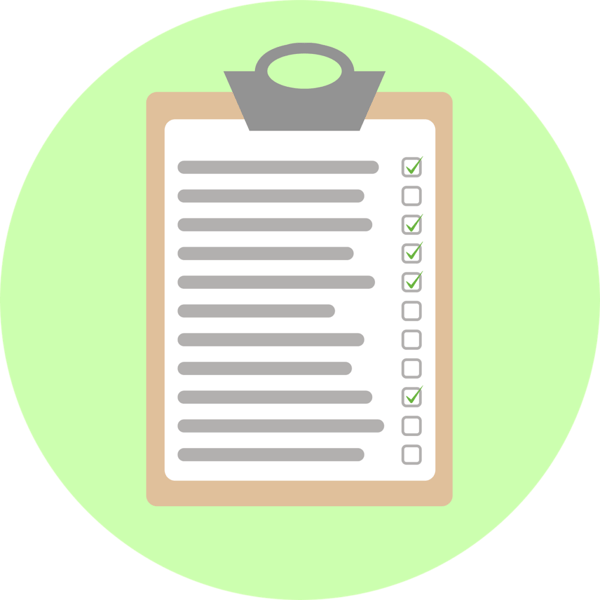
Record Recall Completion
Once the recall has been repaired, it should be noted in the vehicle’s file in the operation’s fleet management software. This will keep the vehicle’s record up-to-date and let the entire fleet operation know the issue has been resolved.
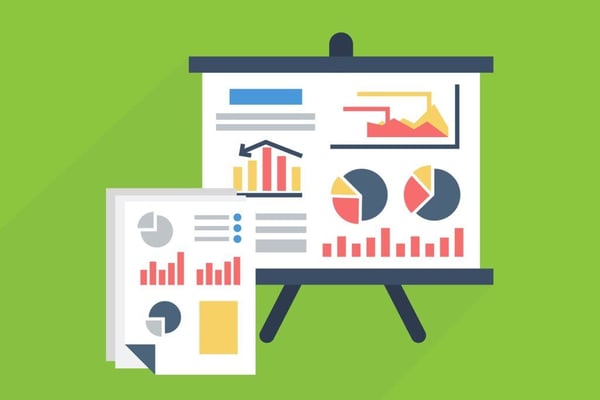
Perform Regular Recall Checks
Fleet operations should run regular reports to determine if vehicles are up-to-date on recalls and if any repairs are still pending. Using a fleet management software system can help fleets store recall information, making it easy to pull reports and monitor vehicle statuses.
To learn how RTA Fleet Management Software can help organize your fleet operation’s recall process, contact us today to schedule a free demo.